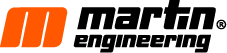
stewardship 2024
Martin stewardship program
At Martin, we relentlessly pursue innovation and continuous improvement to enhance sustainable outcomes for our customers and communities. As global leaders, we deliver safe, groundbreaking products and technologies, driving positive change through responsible stewardship. Our core focus is on improving operational efficiencies, elevating product performance, and prioritizing safety. We enhance our customer success with valuable resources, including the Foundations™ and Safety Books.
The Stewardship program is designed to help our customers improve their processes by offering innovative products and services that enhance the cleanliness, safety, and productivity of their facilities. For our employees, it focuses on refining our processes and becoming better stewards in our communities.
Martin’s Commitment and Stewardship Program
Innovation and Continuous Improvement
-
Focus on sustainable outcomes for customers and communities
Core Values
- Safety, groundbreaking products, operational efficiencies, product performance, and safety prioritization.
- High value on people, honesty, integrity, and transparency.
Customer-Centric Approach
- Dedicated problem-solvers offering tailored solutions and nurturing lasting relationships.
Service Excellence
- Unwavering commitment to driving meaningful change in the industry.
This initiative ties closely with our Why – "To Ignite Excellence so that Families Thrive and Communities Flourish"
Martin is committed to strengthening the communities where we operate, making them better places to live and work. We enhance our workplace culture by fostering a supportive and engaging environment for our employees.
A message from the ceo
For 80 years, our company has thrived on the foundational pillars of people, innovation, and creativity—working tirelessly to make facilities cleaner, safer, and more productive. This mission is at the heart of our existence. Collaborating with our dedicated employees, we are committed to transforming opportunity into action, shaping a future for the next generation. This initiative is deeply connected to our ‘Why Statement’: “Ignite Excellence so that Families Thrive and Communities Flourish.”
For more information on our culture see our culture page:
https://info.martin-eng.com/growing-our-culture-2023
Through our innovative products and streamlined manufacturing processes, we've cultivated strong partnerships with our customers, aiding them in reducing spillage, noise, and pollution in their facilities. Complementing our product offerings, we provide diverse training programs. The FOUNDATIONS™ Learning Center is a hub for bulk material handling articles, and our resources include downloadable E-books, on-demand/live webinars, and the comprehensive FOUNDATIONS™ book series, all geared towards promoting efficient bulk material handling.
Supporting the communities where we operate has been ingrained in the DNA of our family business from the very beginning. Our organizational culture strengthens community partnerships across our 19 locations through outreach and a commitment to sustainability. As a preferred employer, we are dedicated to enhancing employee well-being through competitive compensation, a safe work environment, outstanding benefits, employee activities, and ample development opportunities. We extend a helping hand to those in need, whether it’s assisting an employee in an emergency, supporting neighboring communities affected by disasters, or contributing to children’s and senior homes. Through Martin’s support, we collaborate closely with our employees, who generously volunteer countless hours to assist our community partners.
Our ongoing success relies on our dedicated employees and the strategic use of our knowledge and products to collaborate with customers, enhancing their processes while continually improving our own. As we approach 2025, we are poised to build upon our achievements and further integrate the principles of stewardship for the benefit of our customers, communities, and employees.
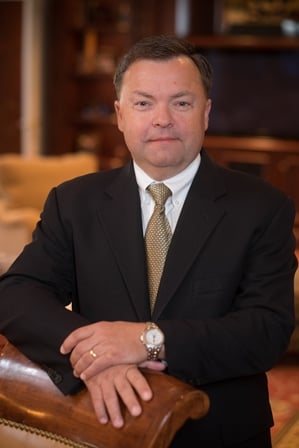
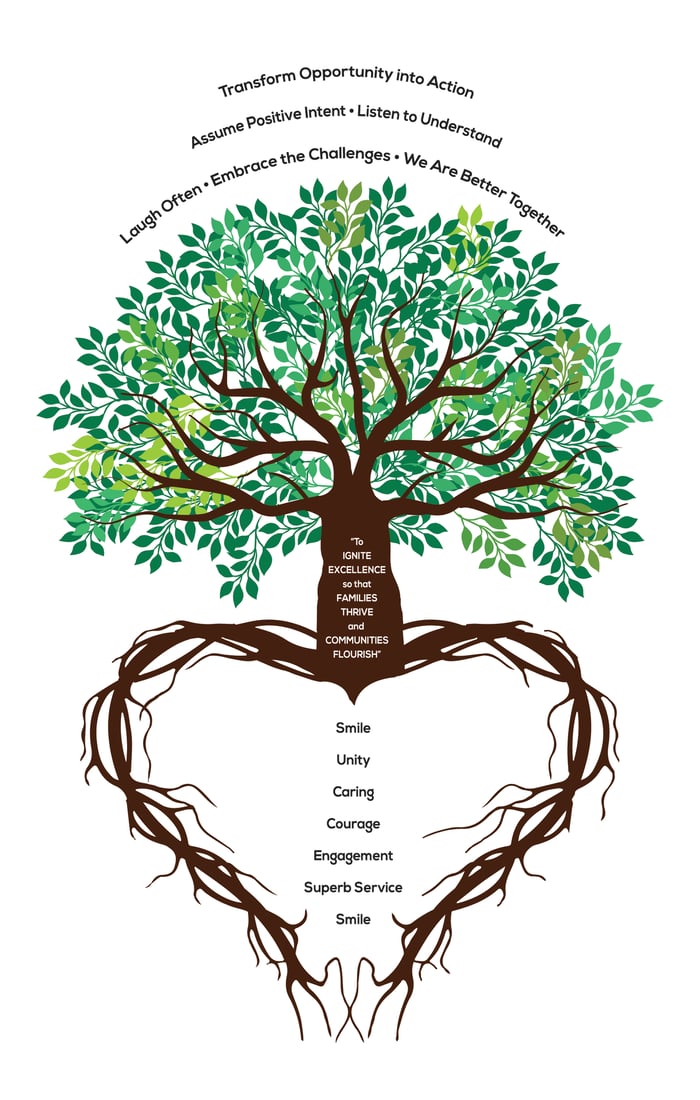
conveyor products
n2
Our continued growth in the N2 product line is saving customers significant time in servicing belt cleaners. In an initial test of 24 cleaners in Europe, we estimate saving 45 hours of service time. Additionally, the reduced need for service van visits has cut fuel usage. This product continues to make customer facilities more efficient and safer.
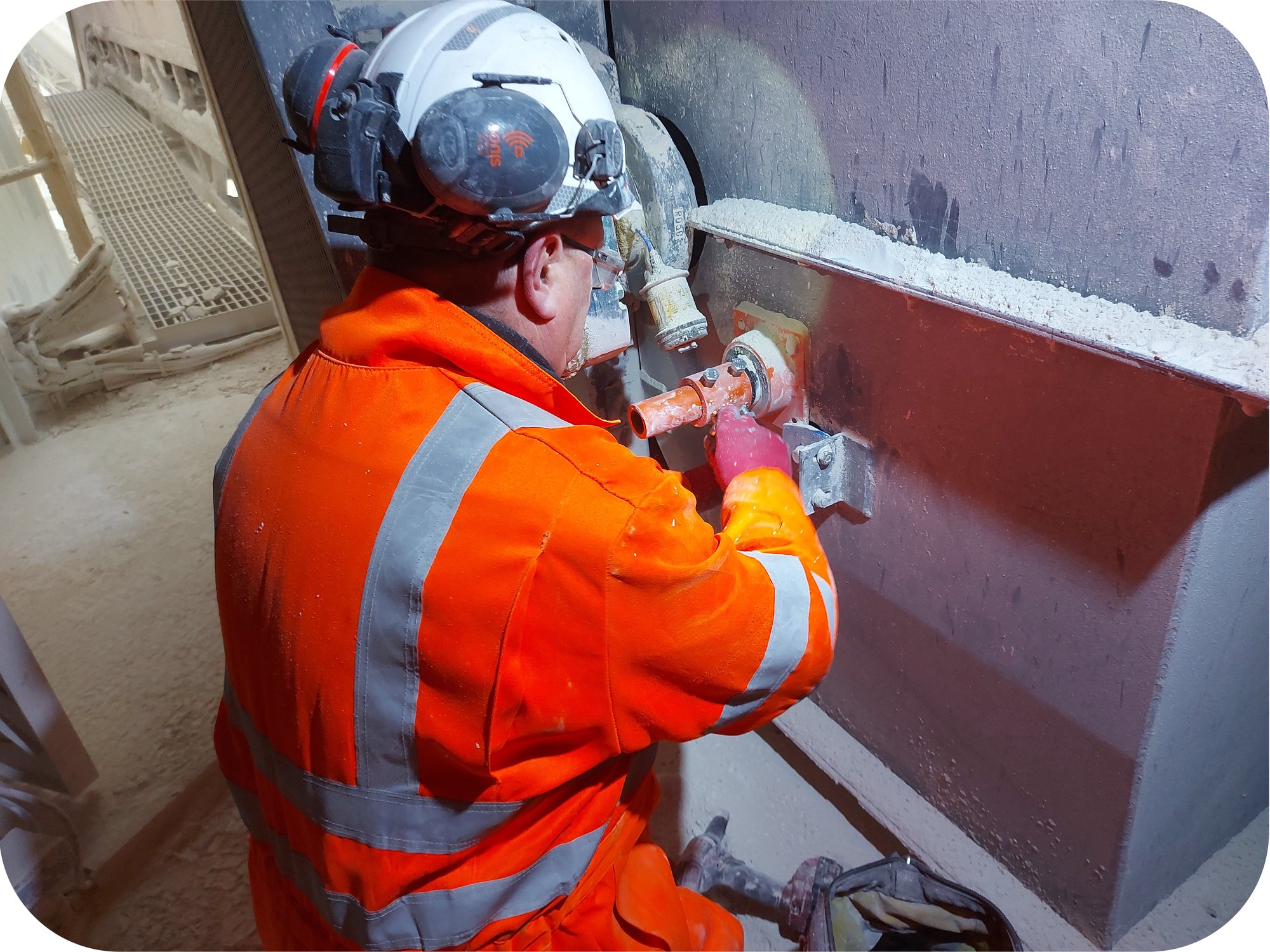
iron ore - brazil
A market leader in iron ore mining faced significant challenges with conveyor belt wear, visible in the support cables. Recurring damage to the aluminum chute of the previously installed scraper negatively impacted maintenance and compromised the blade’s fastening, leading to premature blade wear. This issue directly affected operational efficiency and safety. Martin installed an EcoSafe™ Cleaning system, which offers quick and safe blade changes. The ability to change blades in under 20 minutes provided an efficient and sustainable solution by reducing polyurethane waste.
Before
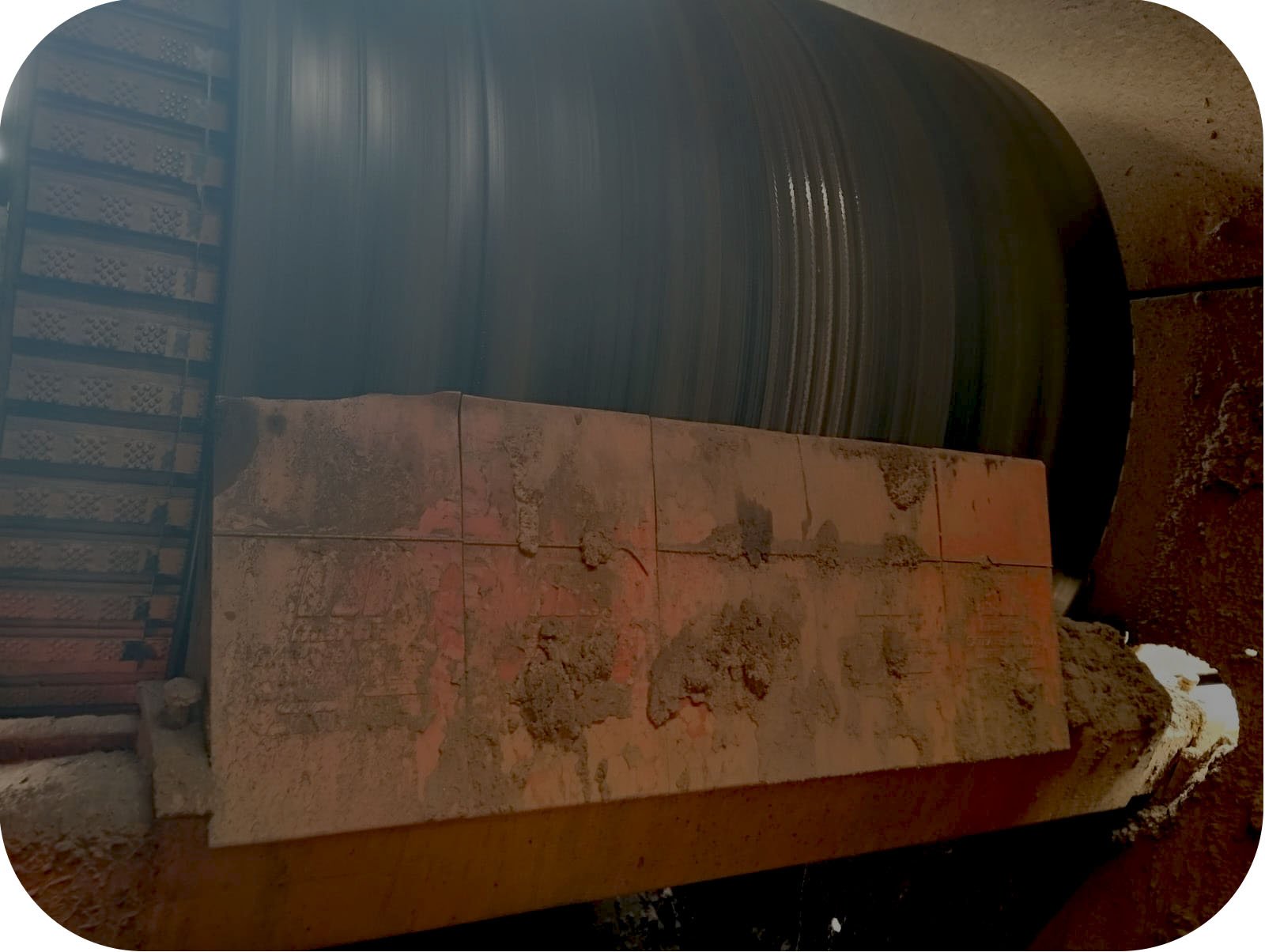
after
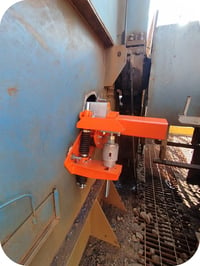
texas
A customer from the Southwest experienced significant spillage, requiring about 20 hours of cleanup each week. We updated their skirting to our Apron Seal™ double skirting, which eliminated the need for cleanup manhours.
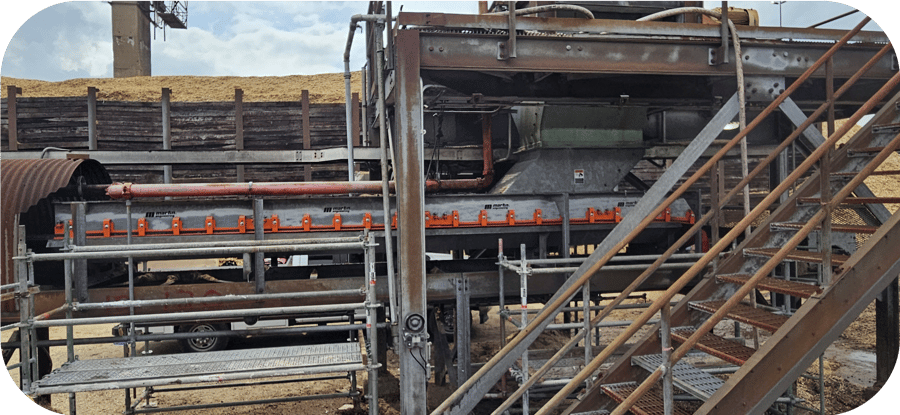
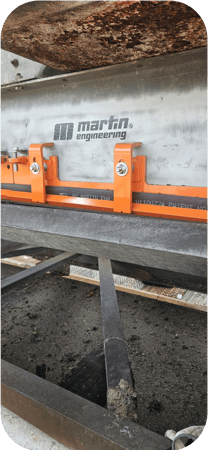
steel
At a steel plant in the Southeast, there was a significant belt tracking problem that threatened to tear up the belt. The Martin Lower HD Tracker™ was installed, and upon startup, the belt tracked to the center, exactly as designed.
Before
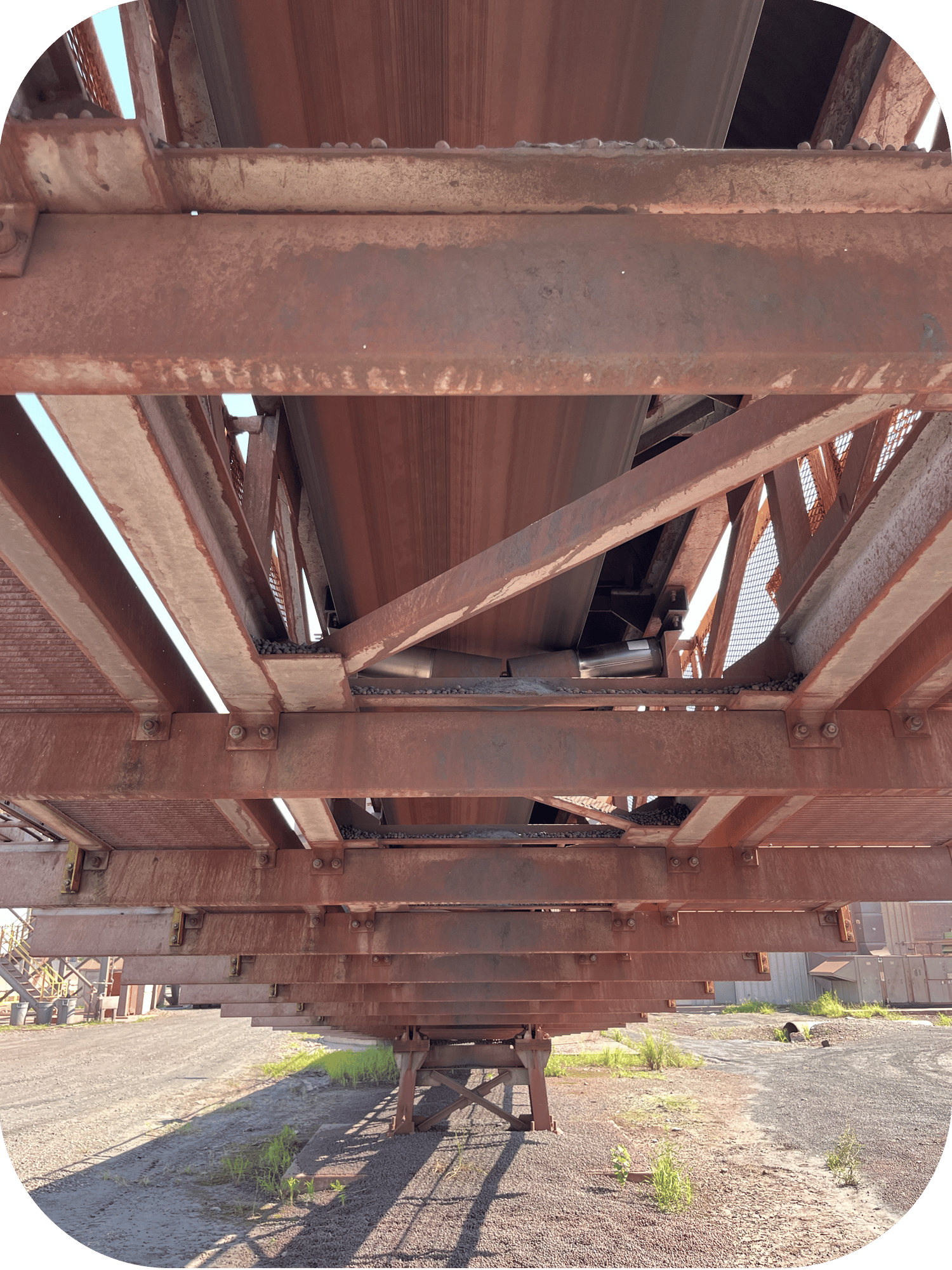
after
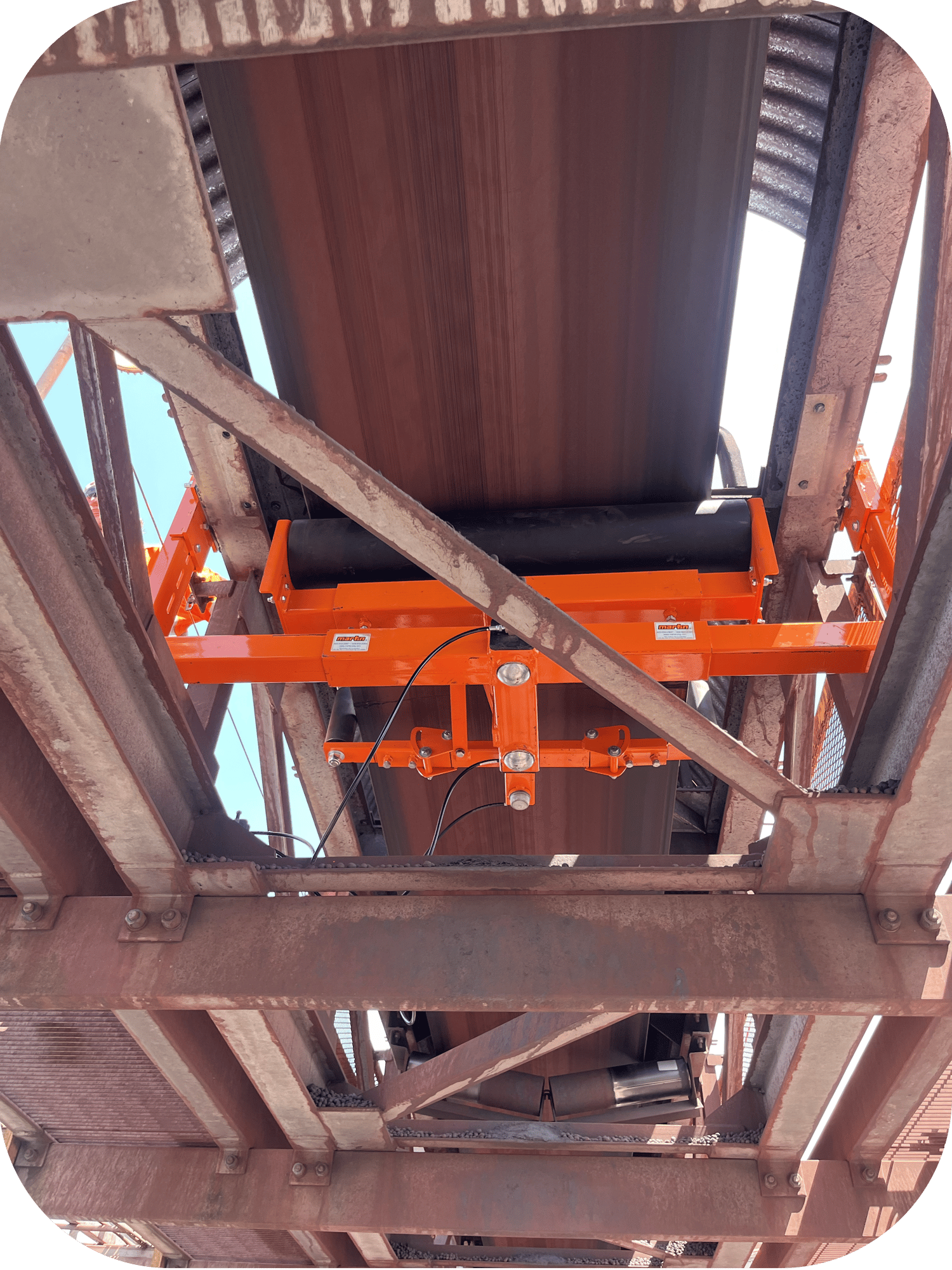
MEXICO
At a customer site in Mexico, we reduced extreme spillage on three belts by installing our QC#1™ Pit Viper and SQC2S. This installation reduced spillage by 108 kg per conveyor per 24 hours.
Before
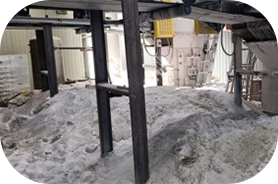
after
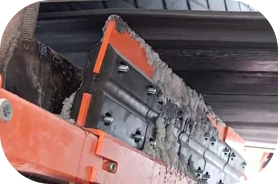
MEXICO
At another customer site in Mexico, an obsolete and misadjusted cleaner contributed to 2,330 kg of spillage over 10 days. We installed a dual cleaning system, including a QC#1PD and an SQC2S™, to achieve better cleaning. This resulted in significant savings, reducing waste and nearly 700 man-hours of cleanup over a year.
Before
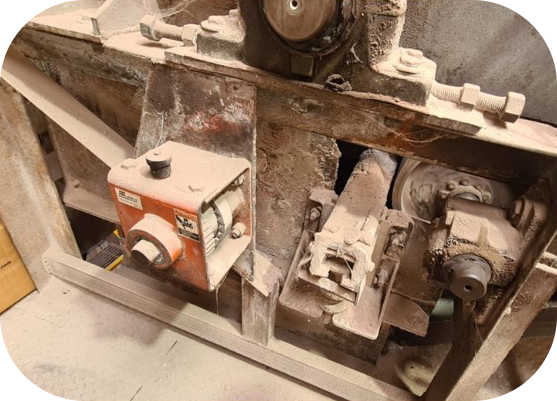
after
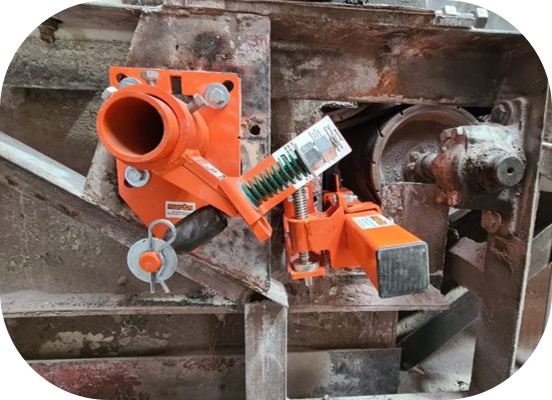
iron ore company in mexico
Poor side sealing, off-center loading, and material entrapment led to premature conveyor belt damage. Martin installed a skirtboard liner and apron seal, which contained the spillage and centered the load, preventing further belt damage. Estimated improvements include saving 90 man-hours and $140,000 in production costs.
Before
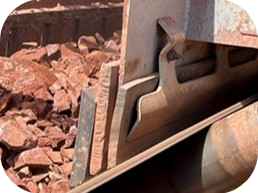
after
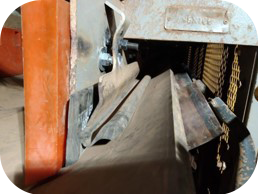
ferrochrome alloy prouction
At a plant in South Africa, a customer had a persistent problem with a transfer point. We corrected the issue by installing Martin® Trac-Mount™ Idler frames to enhance belt support. This minimized dust and potential health hazards for workers, and eliminated material spillage and conveyor belt dragging.
Before
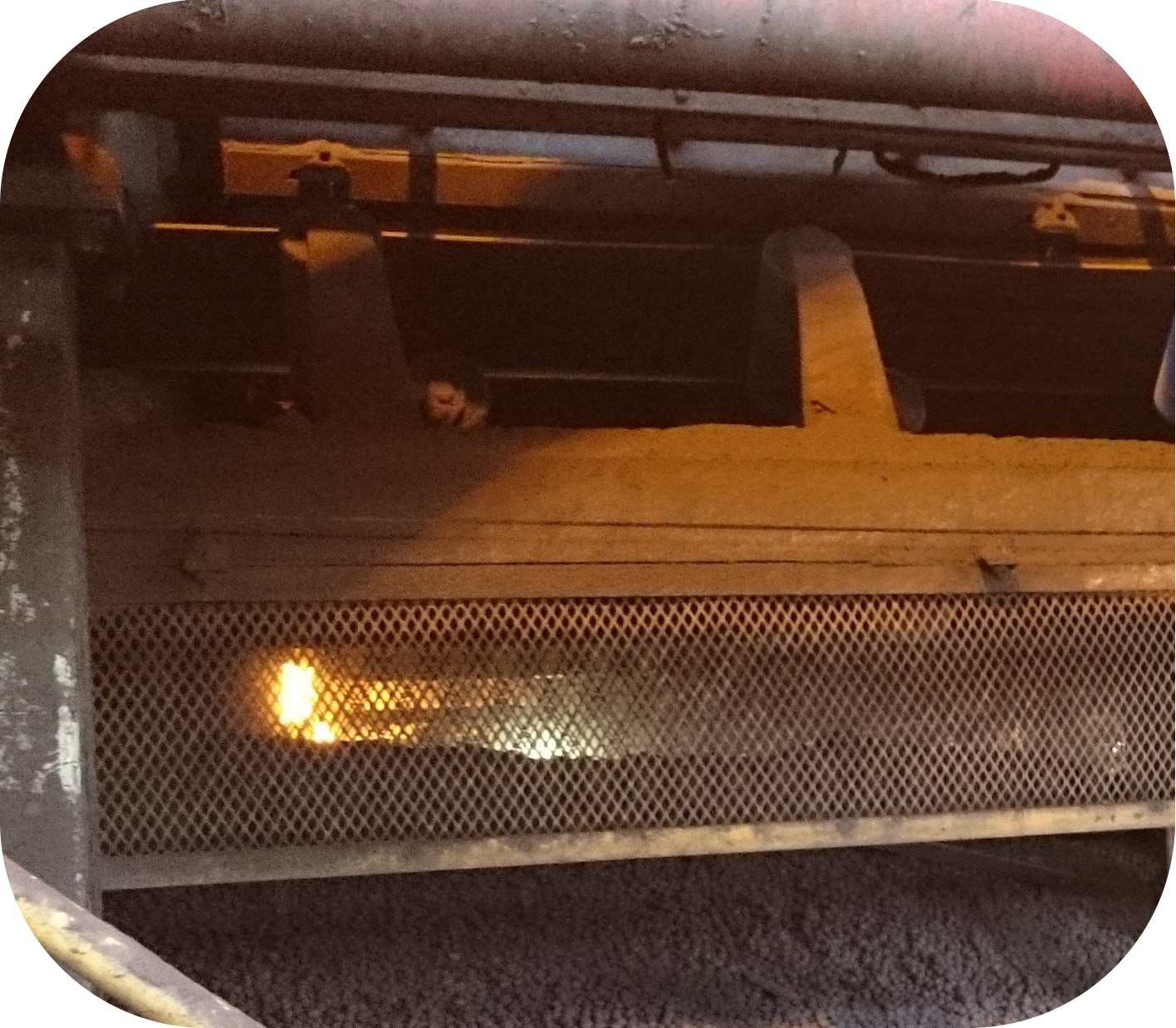
after
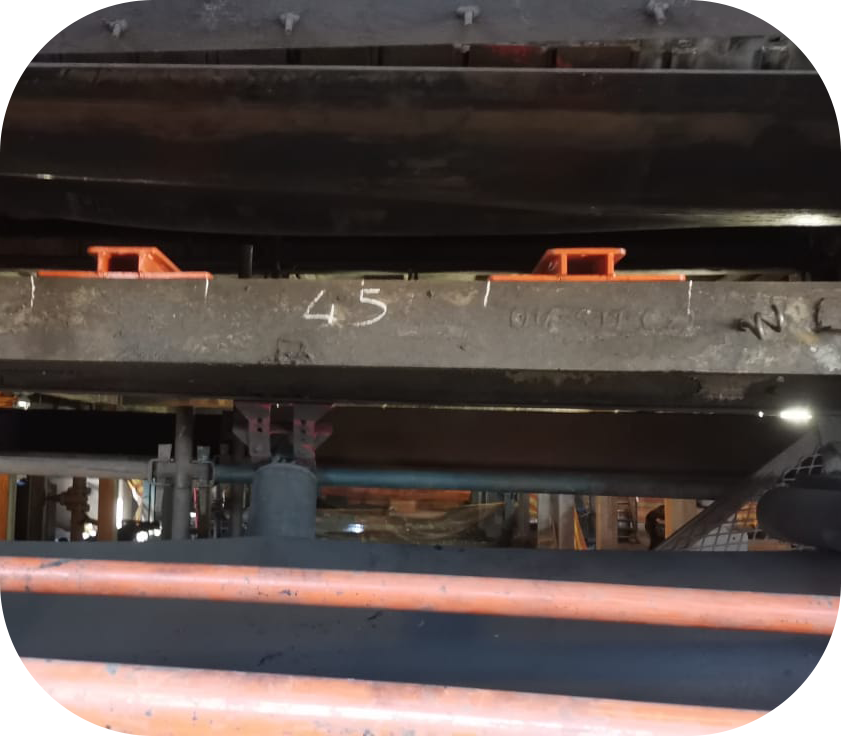
north america
A customer in the Southeast was experiencing so much dust and material loss that visibility was severely impaired when the belt was running. Martin installed our Apron Seal™ and Wear Liner, which greatly improved air quality for workers around the belts and almost eliminated spillage.
Before
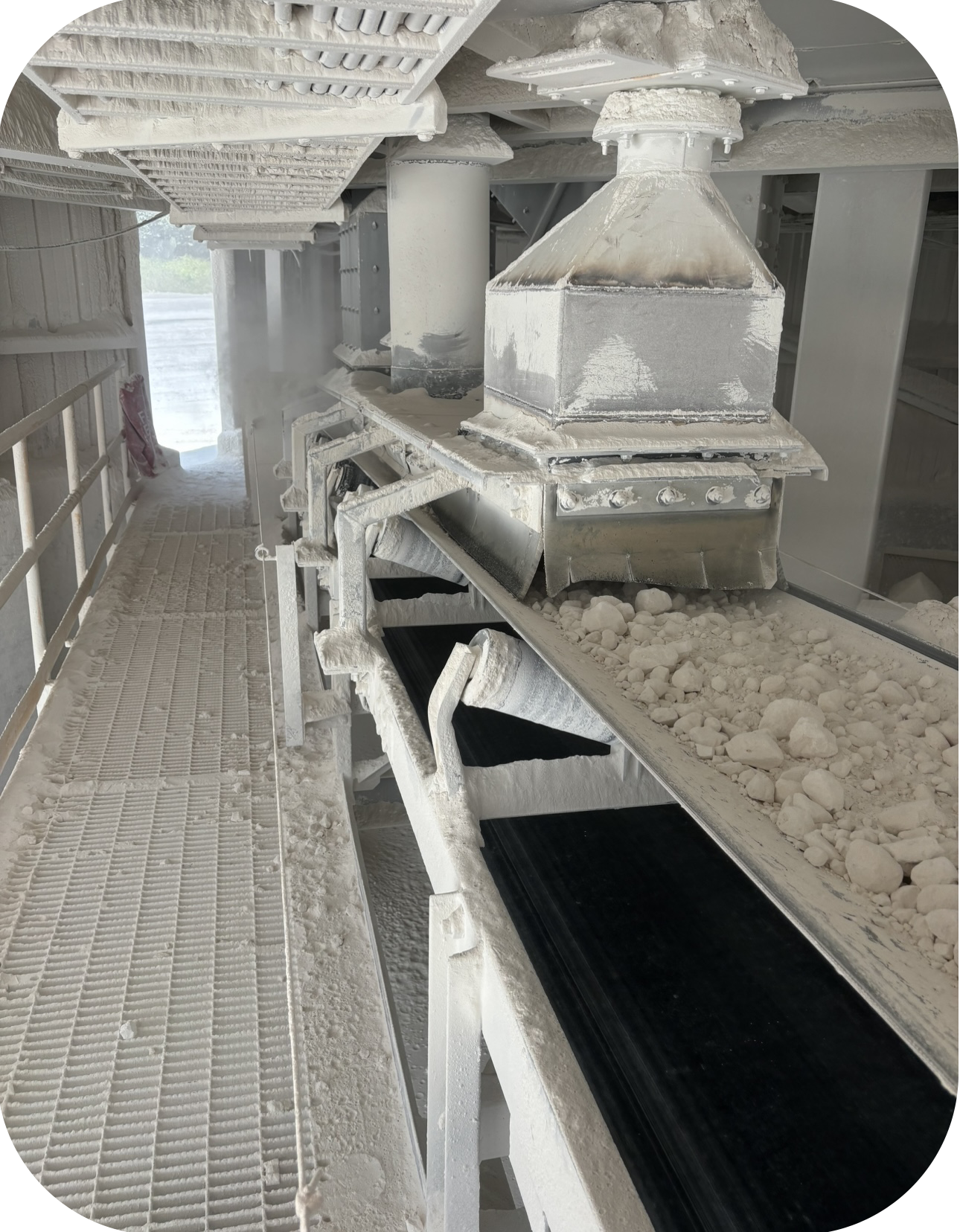
after
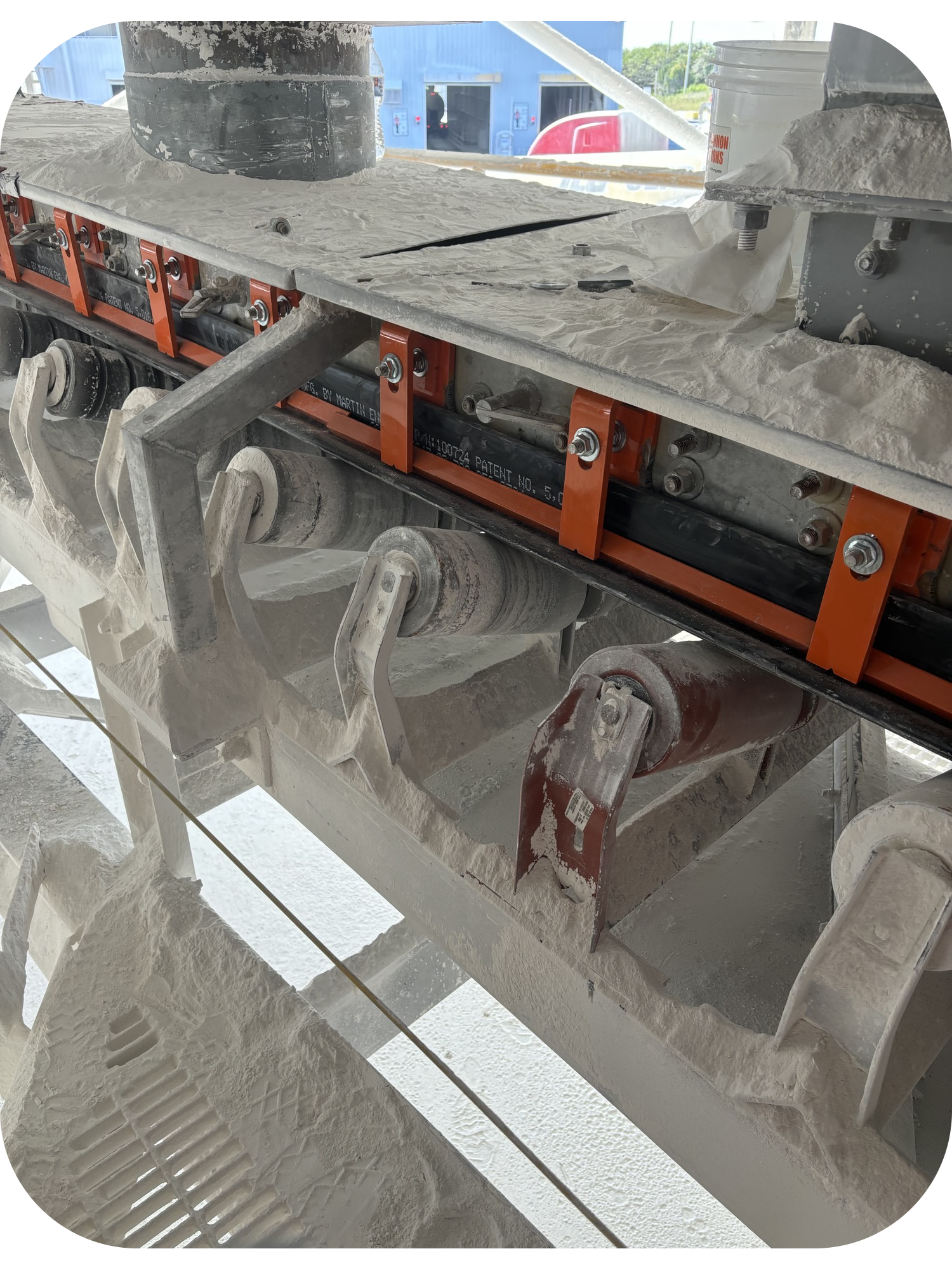
Midwest
At a Midwest facility, we found excessive carryback with sand building up over the year. We provided a secondary tertiary cleaner and plan to install the QC1+ during the third quarter of 2024. The estimated cleanup time savings is at least $5,200 USD. Additionally, a worker was injured during cleanup, so improving safety is also a crucial part of this story.
southwest
A customer in the Southwest had an issue with cleaner installations and insufficient space for an access door. Martin’s new magnetic secondary doors were installed with ease, effectively preventing material from escaping.
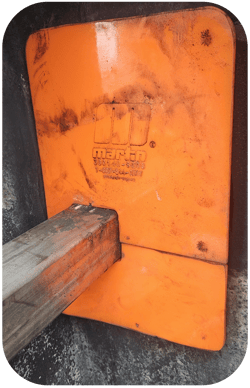
mining company in mexico
A mining company in Mexico faced significant dust issues and was not meeting government standards. A one-year plan to reduce emissions was implemented, including a Dust Suppression System, QC1 HD Primary Cleaner, and SQC2 Secondary System to clean the belts. Additional Trackers™, Impact Beds, and a Torsion Arm V-Plow™ were installed. This resulted in a 90% reduction in dust emissions, improving conditions for workers and the community.
iron ore
A client in Brazil was facing unscheduled stoppages for cleaning and material loss due to spillage. A washbox with a smart sensor was installed, achieving excellent performance with the first blade replacement in 56 days. More importantly, the customer previously had to replace the belt every three months due to wear. Now, they only need to replace it once a year, resulting in a cost savings of USD $360,000 per year.
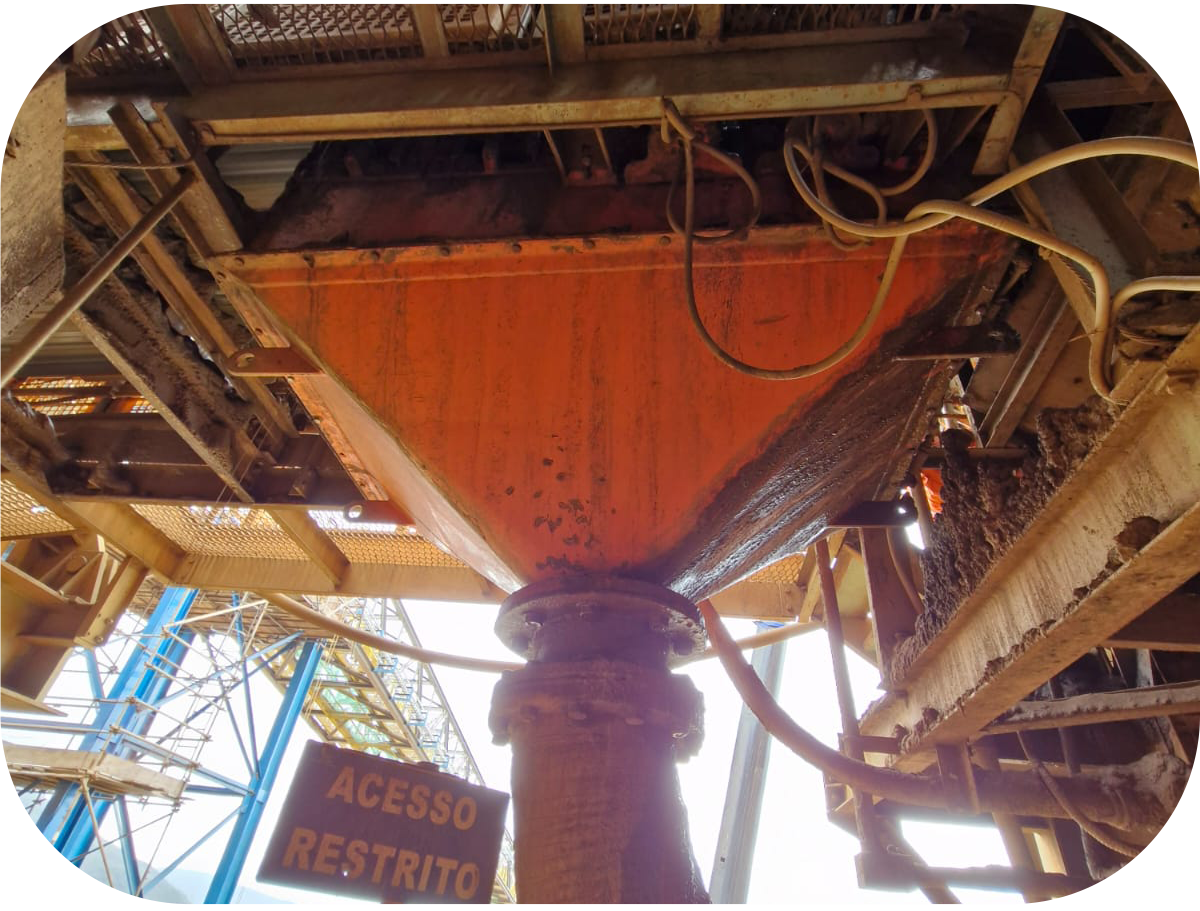
pulp and paper plant in colombia
This customer was experiencing extreme wear on its deflection bars, requiring them to be changed every 30 days. This disrupted the plant’s efficiency and increased costs. Martin installed UHMW bars, which improved performance and extended the wear life to 90 days, reducing the time and cost of changes by two-thirds.
Before
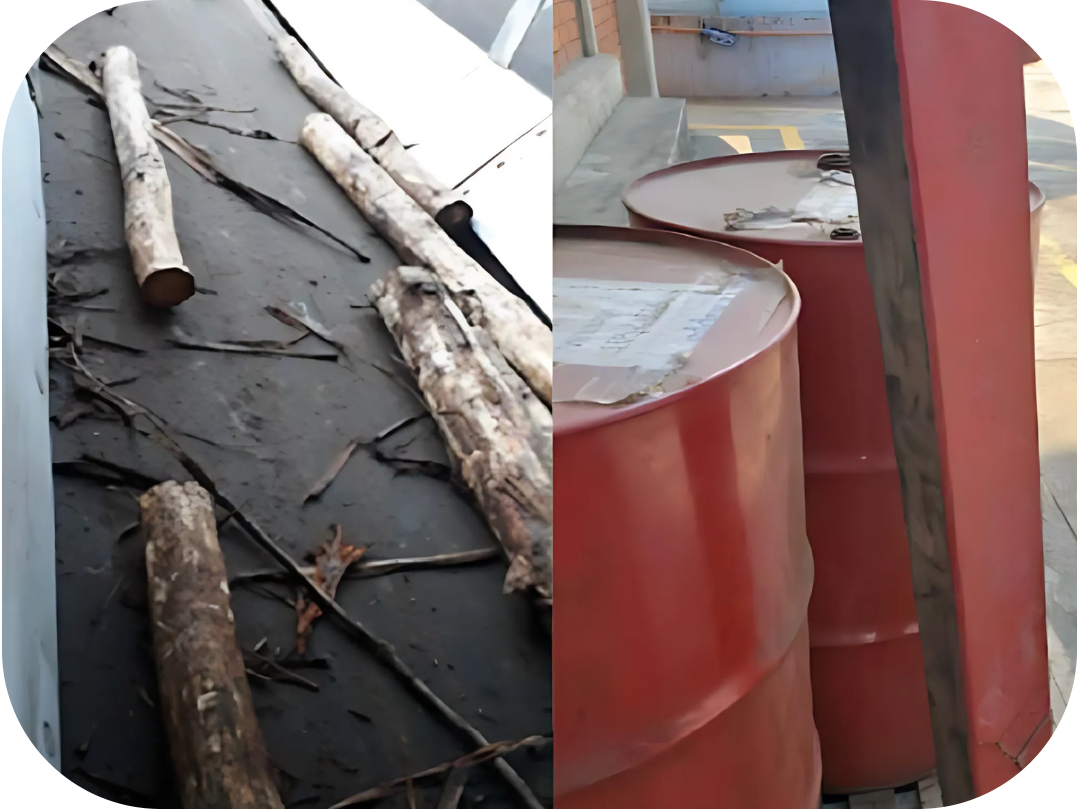
after
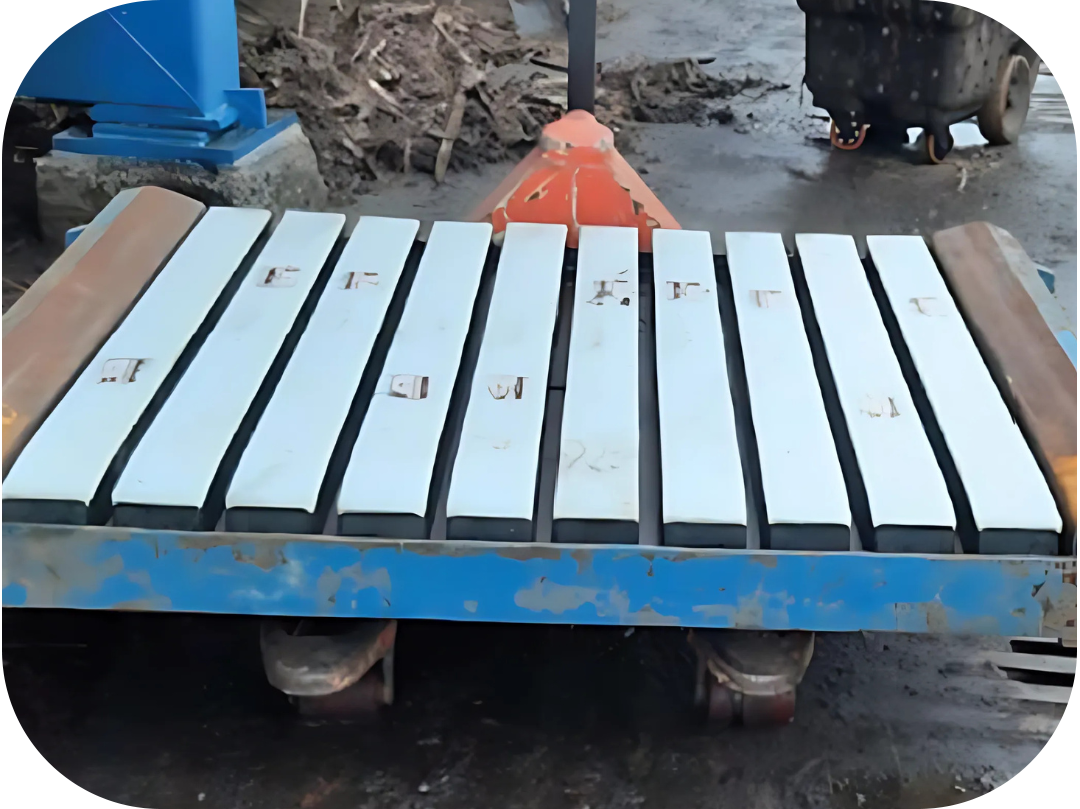
european facility
A facility in Europe processes slag from nearby steelworks into products suitable for road surfaces, thereby conserving natural materials. We installed Guardabelt® to reduce dust emissions during the process, as the facility is located near a recreational area.
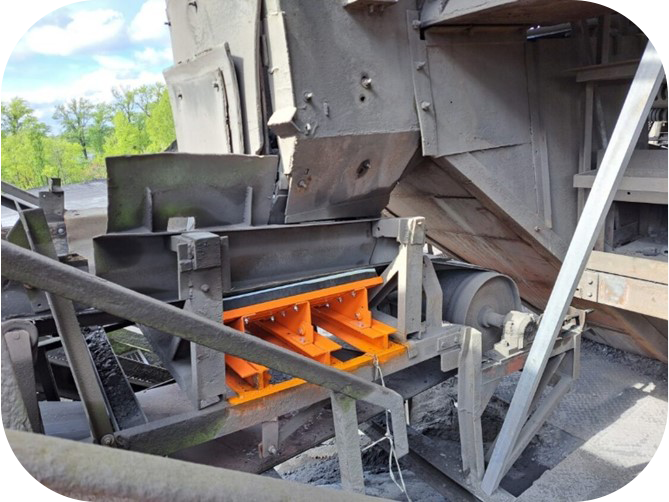
biomass south africa
At a biomass power station in South Africa, the fine wood fiber spillage was making it unsafe for employees to walk. By installing the Martin Chevron Cleaner, the workplace became safer.
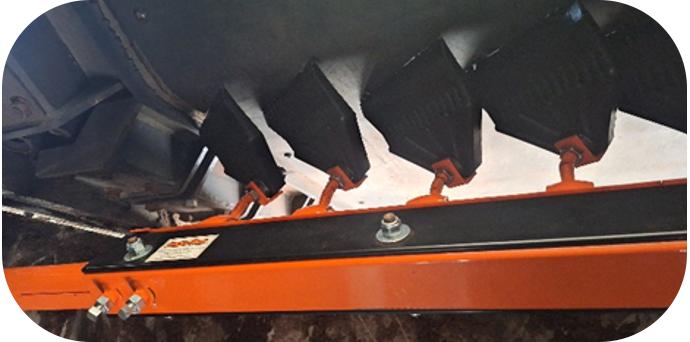
flow aids
niosh award
Martin was honored by the NIOSH Mine and Safety Technology Legislative & Policy Forum. This award recognizes our innovative use of air cannons to remove material from the walls of large aggregate bins in the Northeast, enhancing safety by eliminating the need for employees to enter the bins. We were co-recipients with our customer Tilcon Connecticut, highlighting Martin’s commitment to continuously improving safety and efficiency at customer facilities.
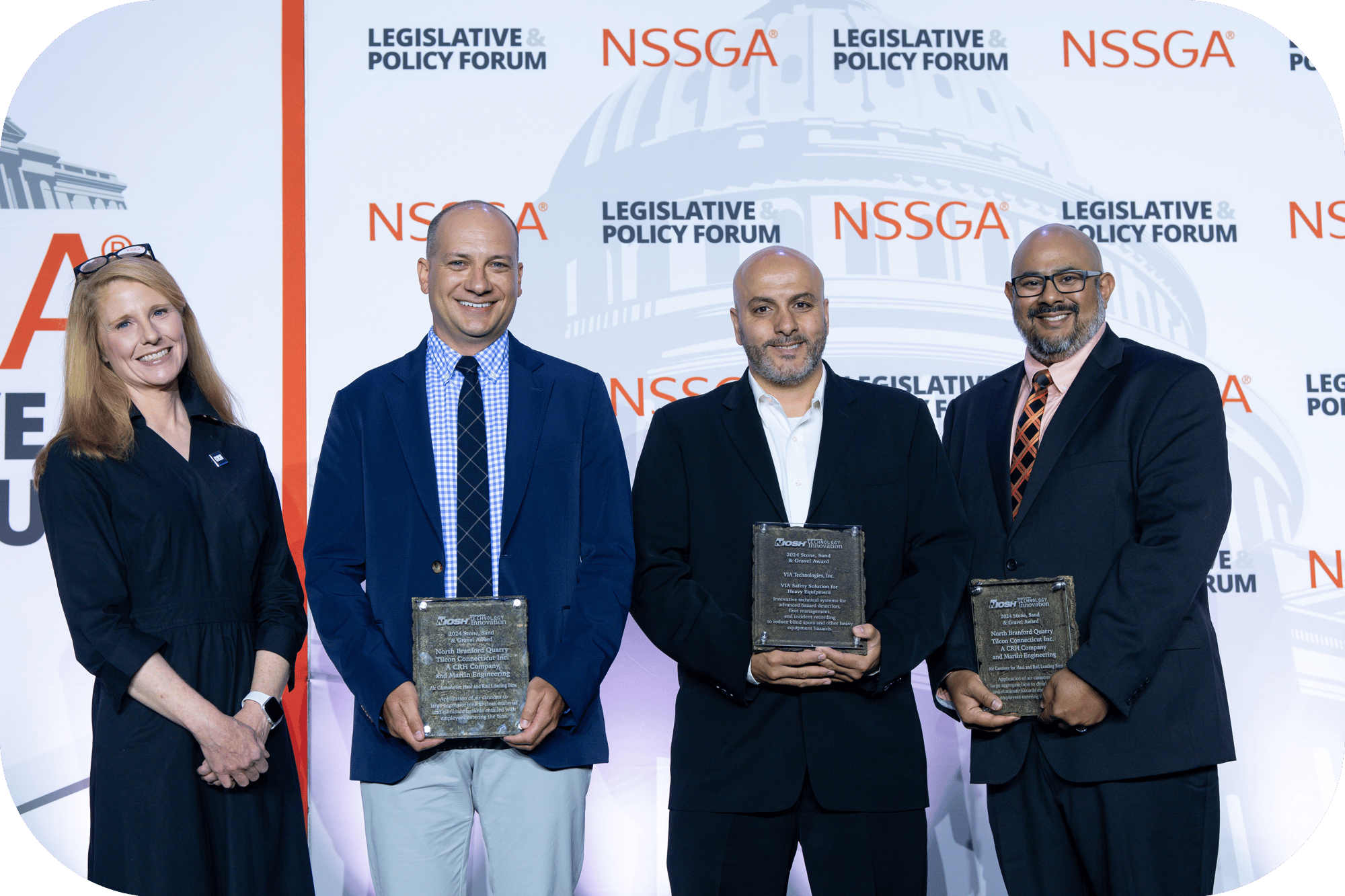
A Midwest company was facing chute plugging issues that other methods couldn’t fix. After installing 2 air cannons, cleanup time reduced from 2-4 hours a day to just 5 minutes once a week. Plans are underway to continue improving material flow and add air cannons to other areas. That's a remarkable improvement! from the walls of large aggregate bins in the Northeast, enhancing safety by eliminating the need for employees to enter the bins. We were co-recipients with our customer Tilcon Connecticut, highlighting Martin’s commitment to continuously improving safety and efficiency at customer facilities.
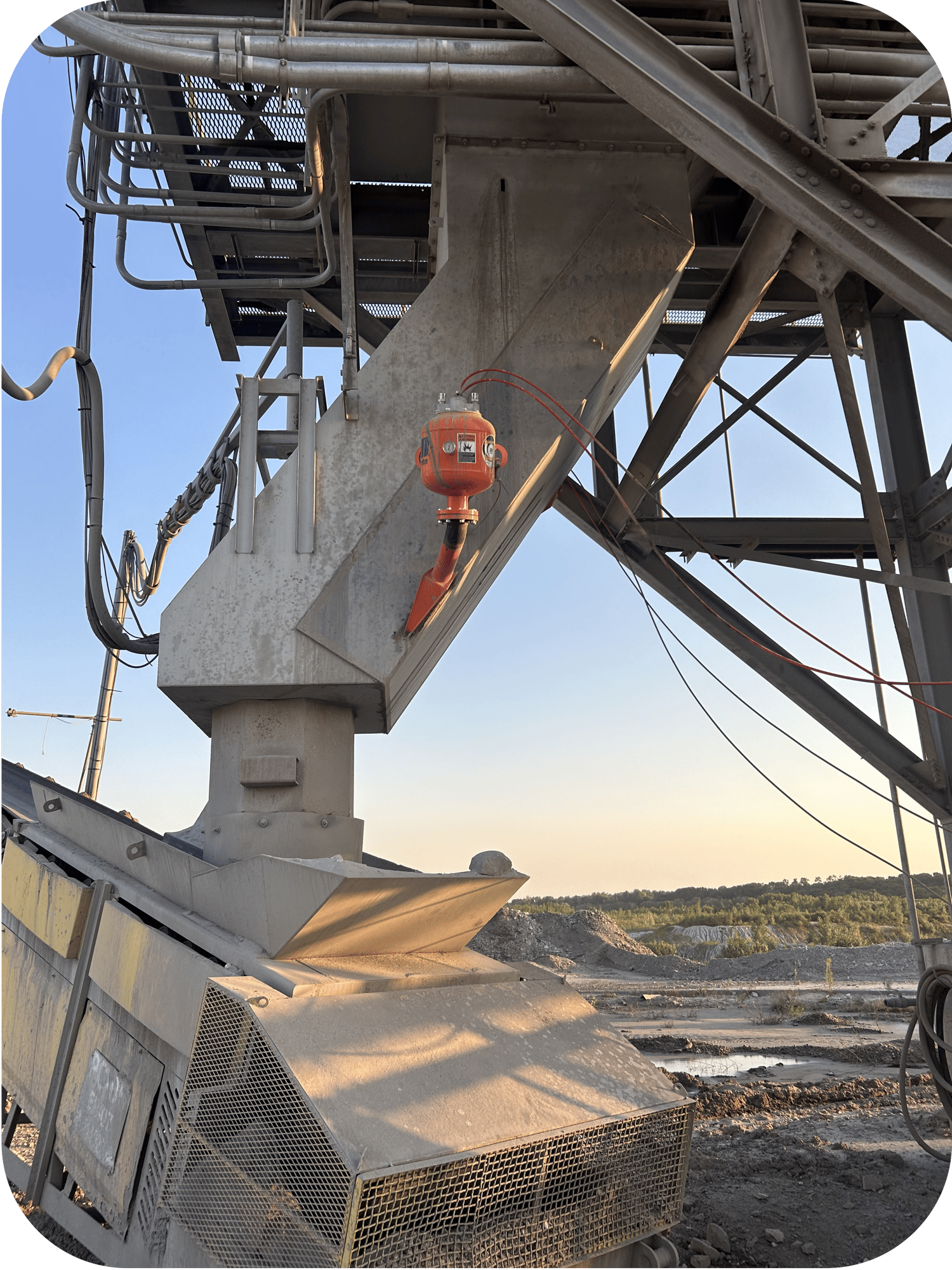
colombia
A company in Colombia faced major flow blockage issues. After installing six Hurricane 150 L cannons and testing various cycles, a blend of automatic and manual launches achieved 90% fluidity in the hopper, vastly improving operational efficiency.
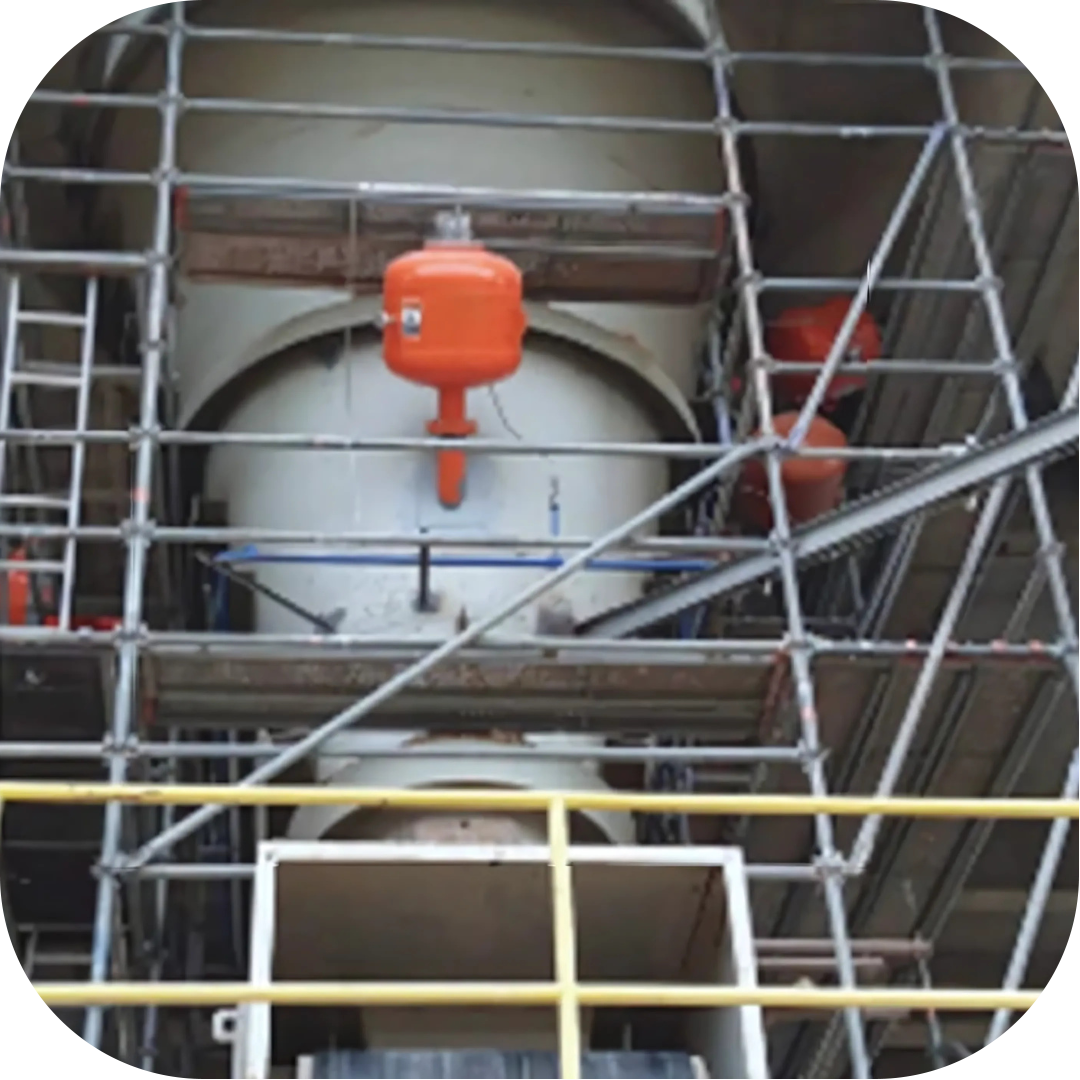
brazil
A large mining company was dealing with frequent build-up issues, leading to 10 daily stops to clean and unclog the system, which posed risks to employees. Martin installed Hurricane Air Cannons and Arcoplate™ wear plates along the chute, eliminating the clogging points. This allowed the company to maintain continuous operation without interruptions.
peru
A mining company dealt with hopper blockage due to sticky material, compounded by hopper design issues. Martin installed 24 Hurricane Air Cannons at strategic points across six transfer hoppers. The automation of PLC Panels kept hoppers free of material build-up, minimizing the need for human cleanup intervention.
Before
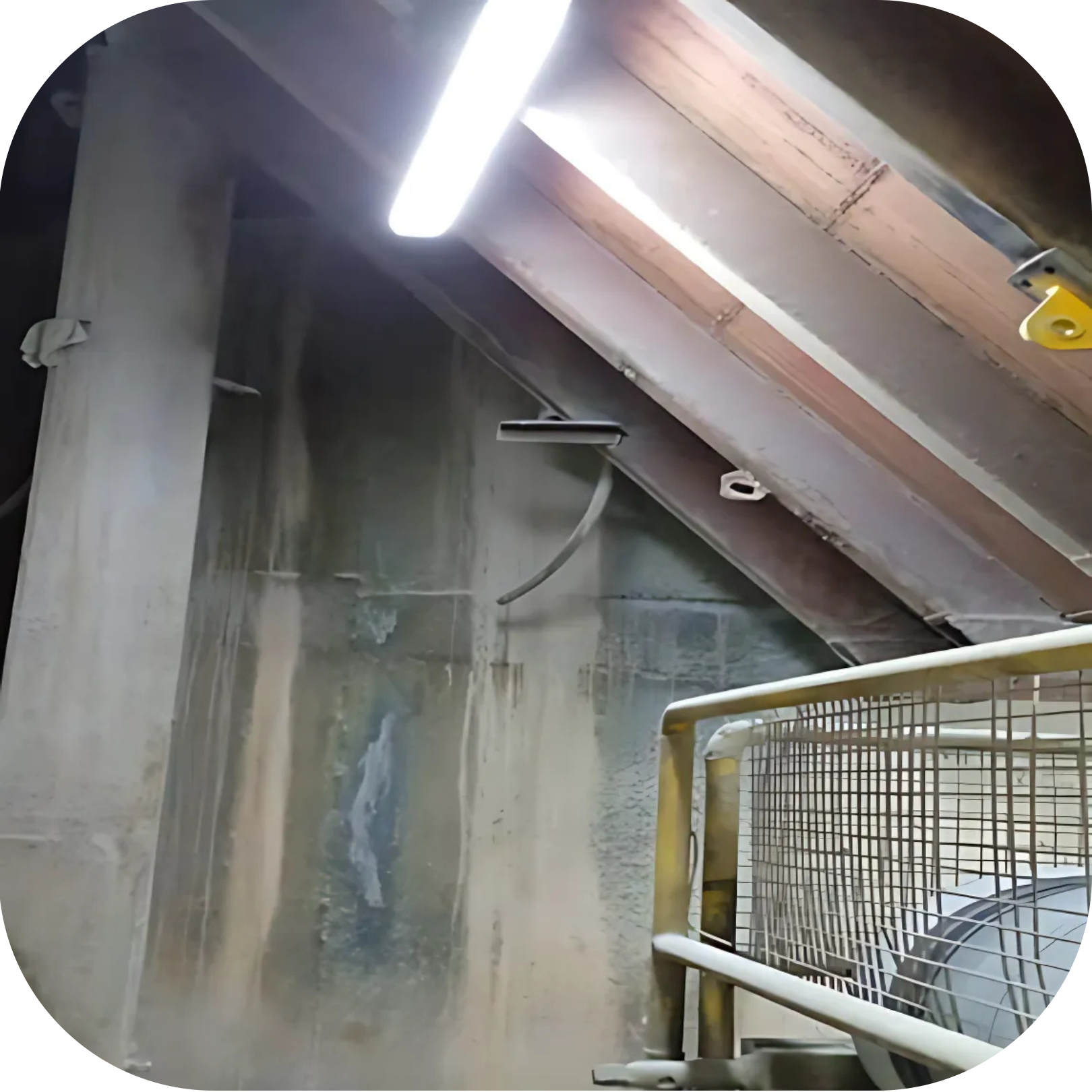
after
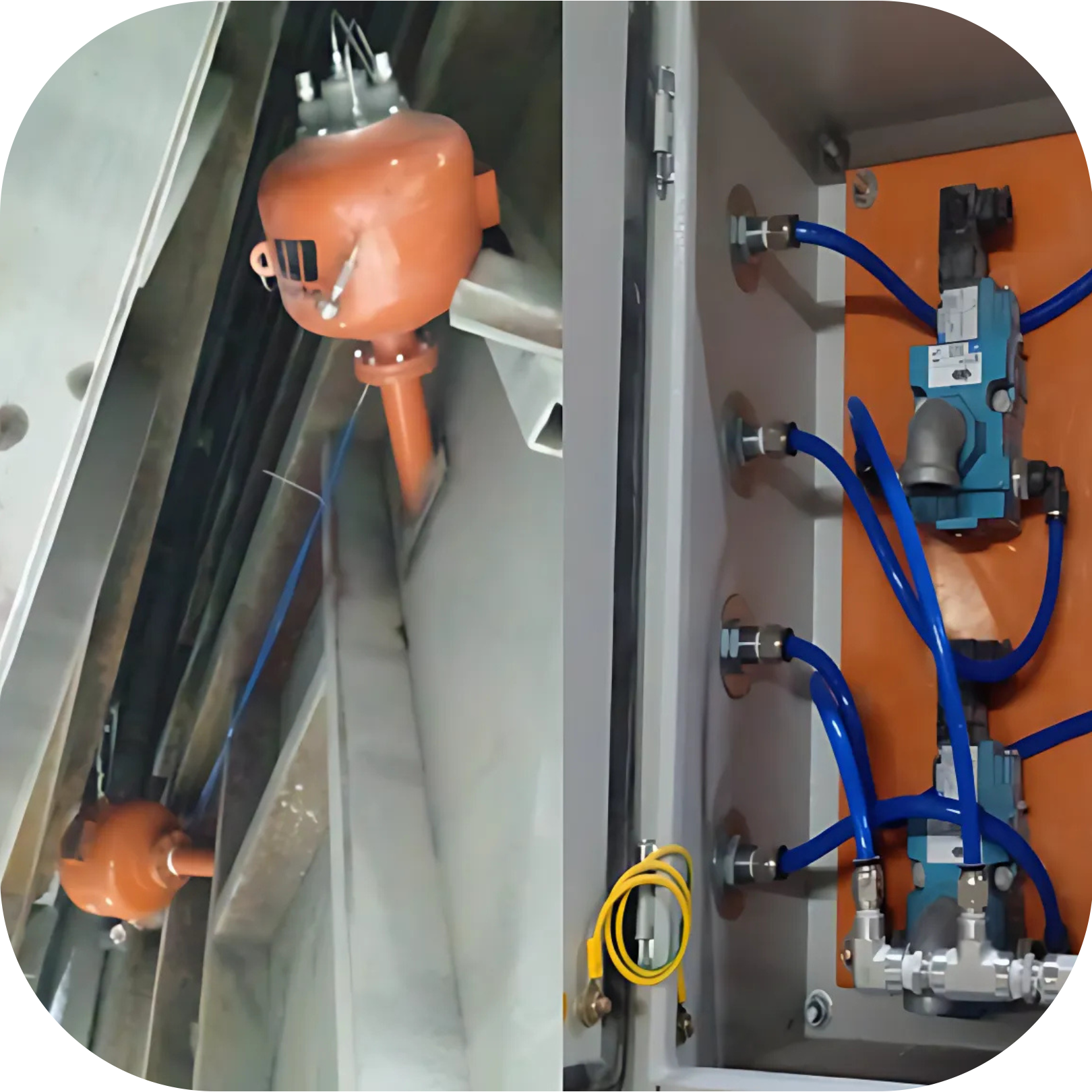
mexico
At a large cement plant, only 70% of the cannons were operational, reducing production by 20% and causing 2 hours of daily maintenance. After a series of upgrades, productivity increased by 25%, and maintenance time was eliminated.
Before
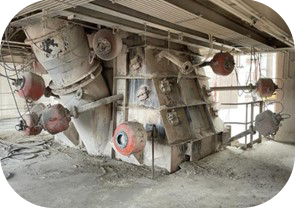
after
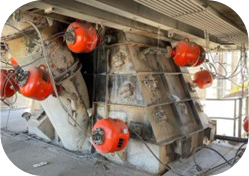
Europe
A customer in Europe faced a common issue in the recycling industry: clogged ducts that required manual cleaning, which exposed employees to potential hazards. Martin installed the Hurricane® Air Cannon, which effectively removed flue gases and suspended particles, clearing the exhaust duct. As a result, manual cleaning has been significantly minimized.
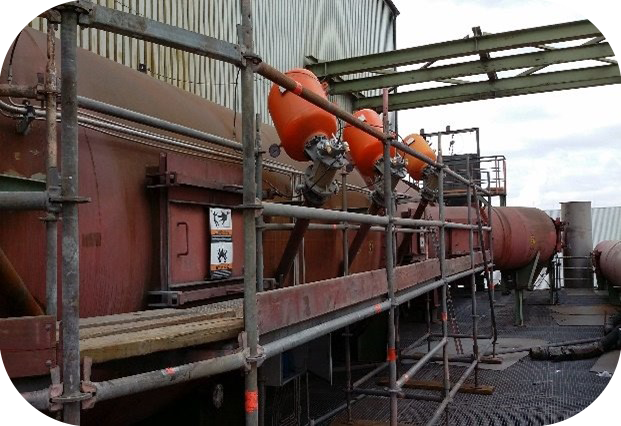
india
A steel plant in India faced hard build-ups and silo jamming, leading to production losses and cleanup challenges. Martin installed nine 70L Martin® Typhoon Air Cannons with SMART™ nozzles, providing powerful yet efficient performance. Over the year, material flow has increased significantly, and the high-risk task of eliminating blockages has been greatly reduced for employees.
Before
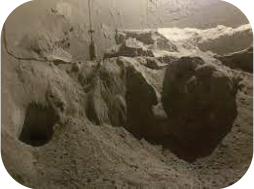
after
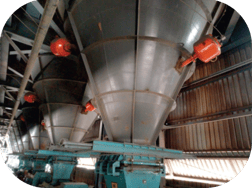
mexico
At a facility in Mexico, a poor filling process was causing spills, downtime, and unsafe conditions. An MT Fast vibrator with a vacuum mount was installed, allowing for optimal material loading.
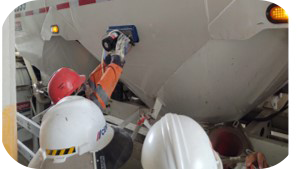
Mid Atlantic State
At a precast plant in the Mid-Atlantic states, Martin was called in to replace underperforming vibrators. Two counter-rotating electric vibrators were installed, producing twice the force of the total mass of the table, mold, and concrete mix.
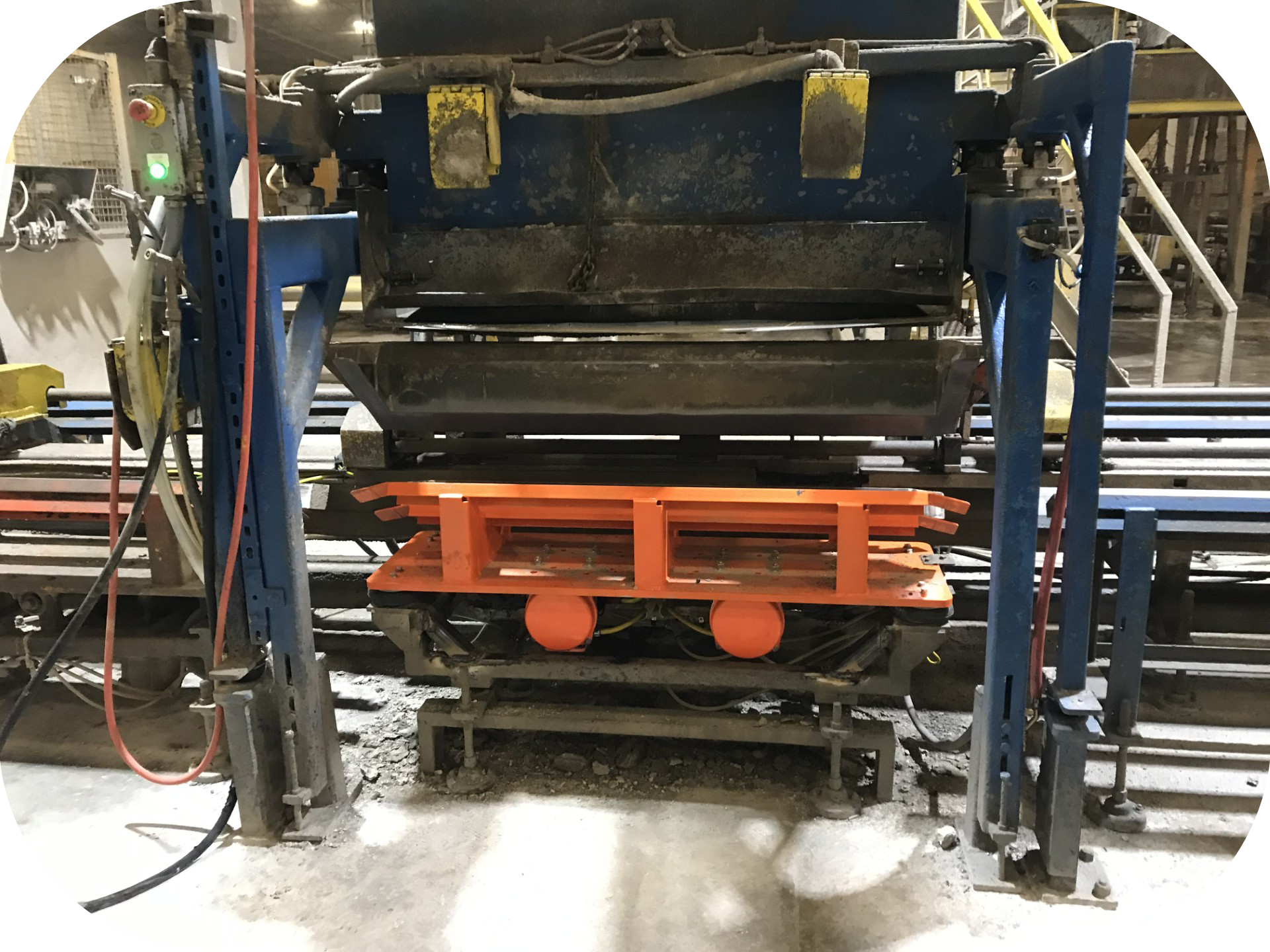
In 2024, we continued leading Foundation webinars for customers, offering 66 live classes and 3 virtual ones, with a total of 1,600 attendees. These classes are highly sought after, educating our customers on all aspects of belt conveyors. Additionally, 11 webinar sessions were offered, attracting nearly 1,000 attendees.
In Mexico, we provided 32 hours of Foundations Training to 70 people. This training enabled the trainees to identify issues in their own facilities and seek solutions.
In the USA, we've recycled 1 million lbs of scrap steel, alongside 50,000 lbs of aluminum, 31,000 lbs of stainless steel, and 35,000 lbs of paper/plastic. Major steps toward sustainability.
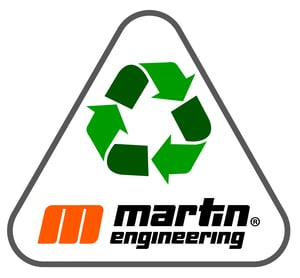
Building on the USA's urethane department initiatives, EMEIA launched a project to reduce urethane scrap. Germany, Turkey, and India focused on minimizing waste during blade cutting, achieving over a 90% reduction. In South Africa, the initiative also targets waste reduction in blade cutting and the pouring process. The South African project is progressing well, and we will continue to push forward with these efforts.
Those N2 sensors have been a game changer, saving around 20 minutes per cleaner and accumulating a total of 6,460 minutes in service time for our customers this year. That's a significant efficiency boost indeed!
community
In the USA, we contribute around USD 1,700 per employee. Globally, our community contributions amount to USD 185 per employee.
We have 7 employees in the US who volunteer countless hours to the Martin Motion robotics team. This effort benefits local high school students to participate in the FIRST robotics program. The students participate by evaluating the game, building the robot, developing the strategy to complete at a local and possibly a national level.
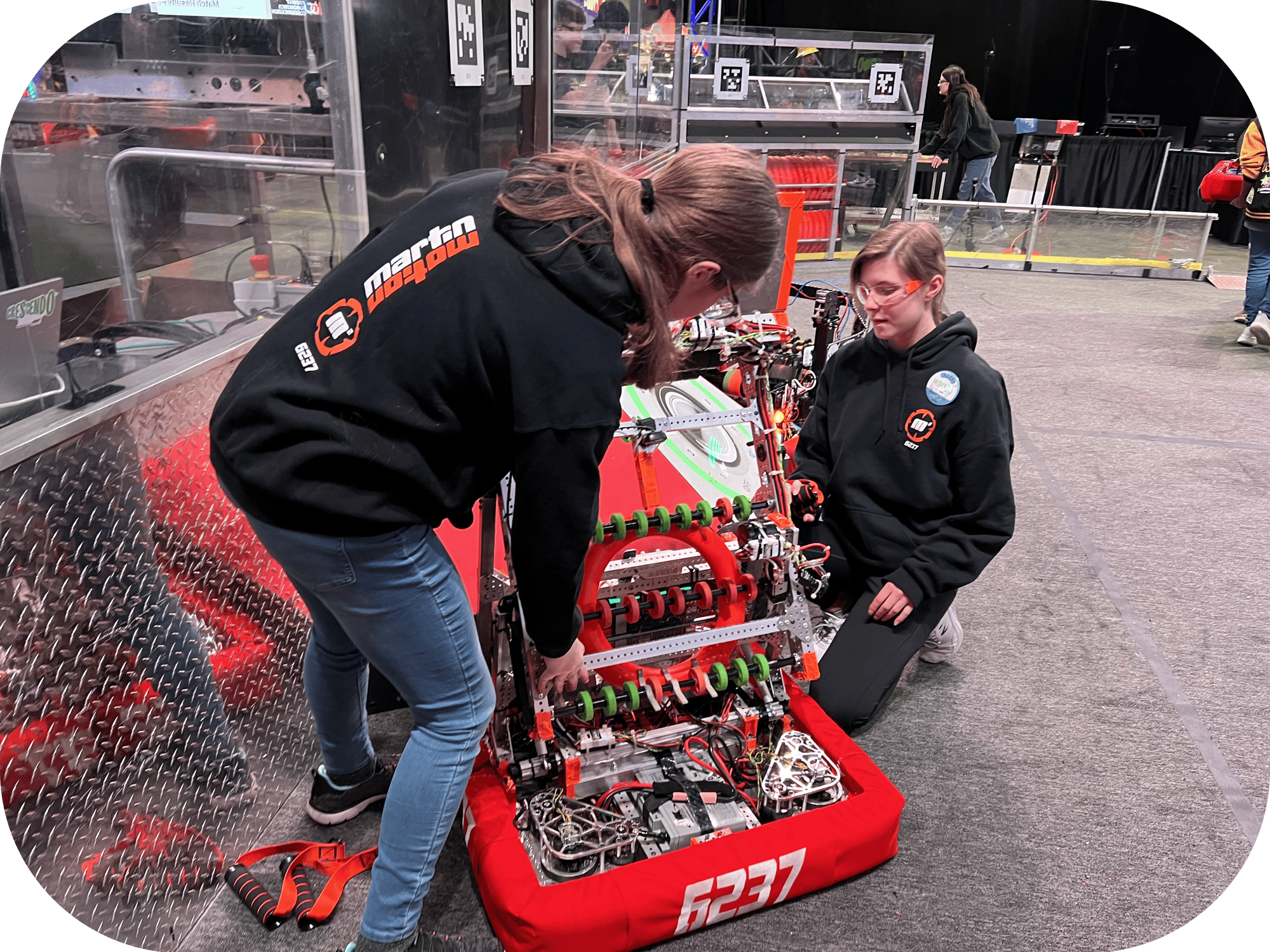
Casa Hogar Orphanage
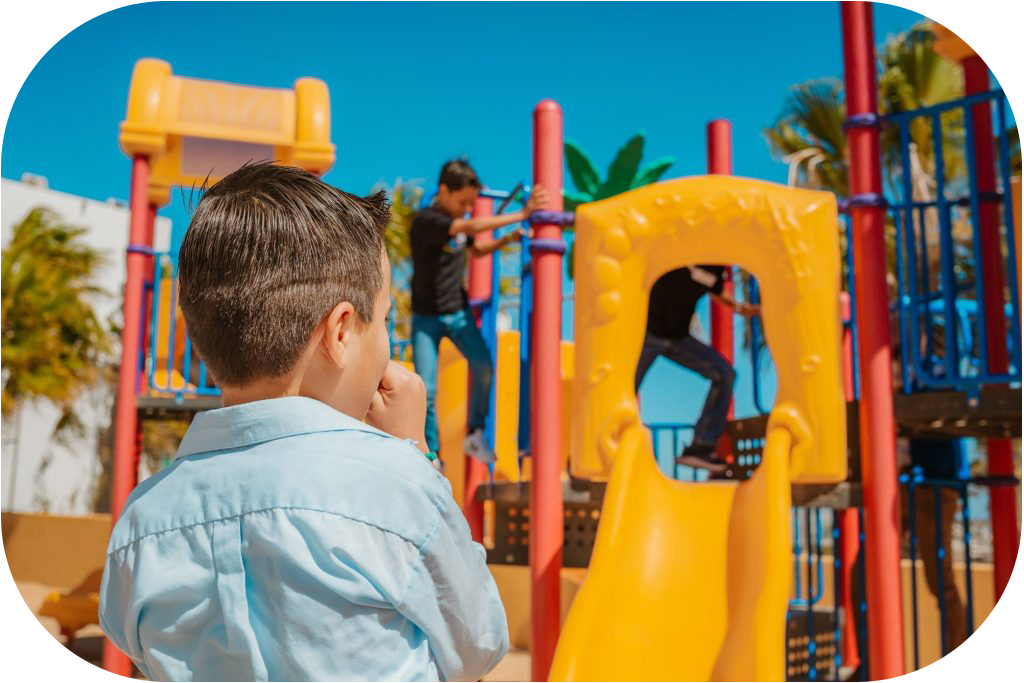
Red Cross - several of our units hold Red Cross Blood drives to support their local need - “ensuring that our communities flourish”
%2015.10.58_d5f1cff2%20copy.jpg)
Pay it Forward for Communities - Turkish team hosts clean up of local industrial area
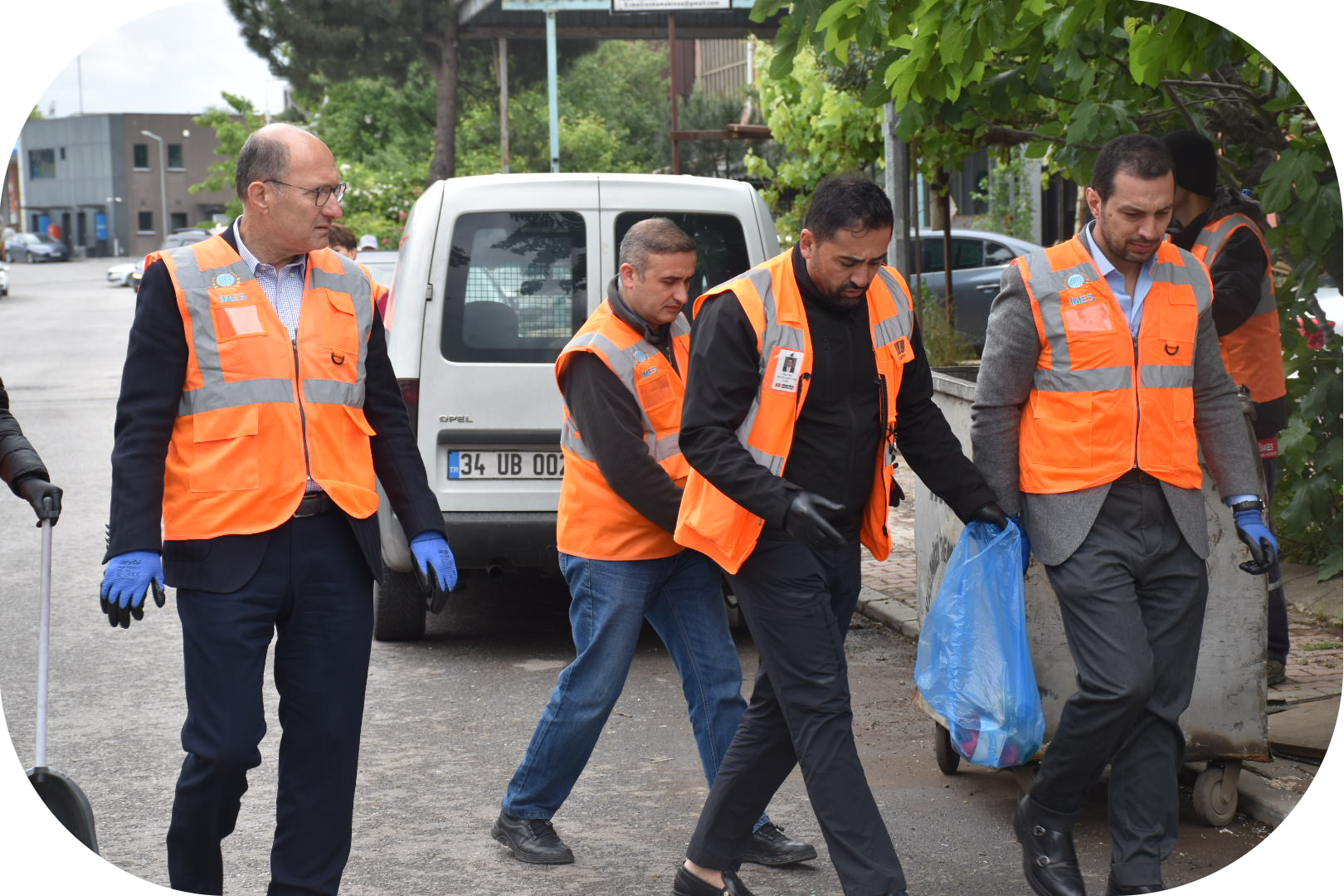
Junior Achievement
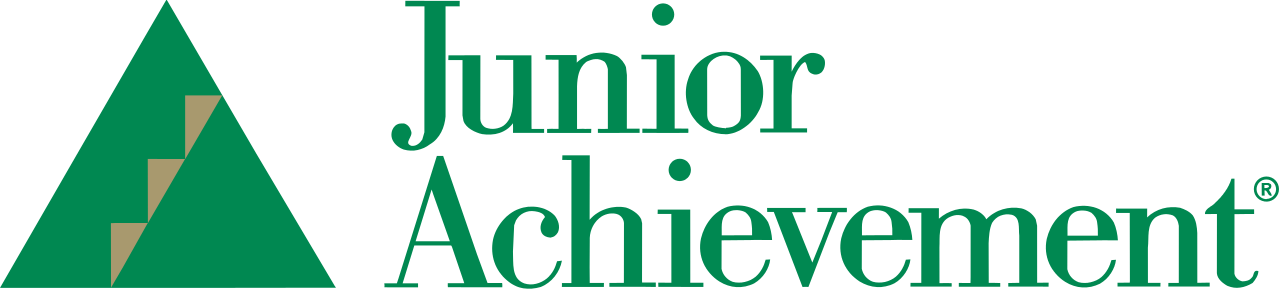
Hog Capitol Wildlife Rescue and Rehab
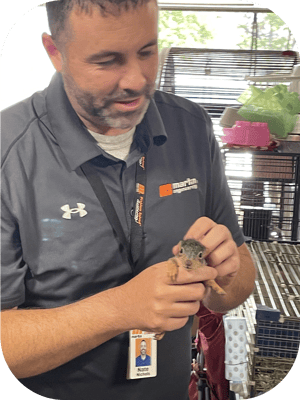
Our Financial Manager of Martin Engineering Africa, saw a chance to make a real difference through education. She unexpectedly met a couple who needed support to further their education. Martin stepped in and helped fund a Bachelor's degree for the wife and a Project Management course for the husband. It's incredible to see how education can change lives!
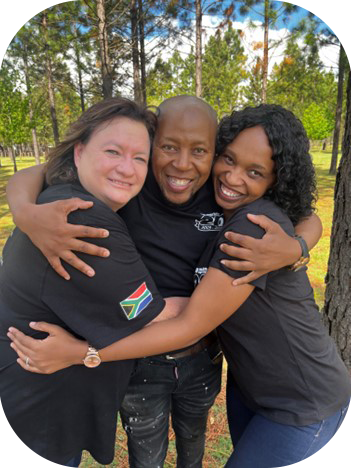
St. Jude’s Foundation – Chicago Marathon
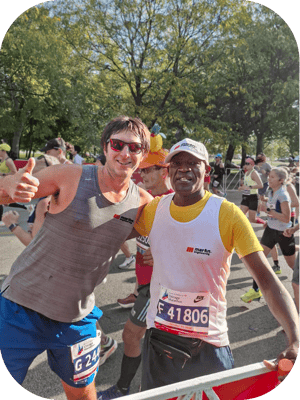
In the USA and Mexico, we conduct 'Pink' campaigns, which involve selling pink products and raising funds for breast cancer awareness organizations. Last year our efforts in the US raised over $12,000 for the Susan G. Komen organization.
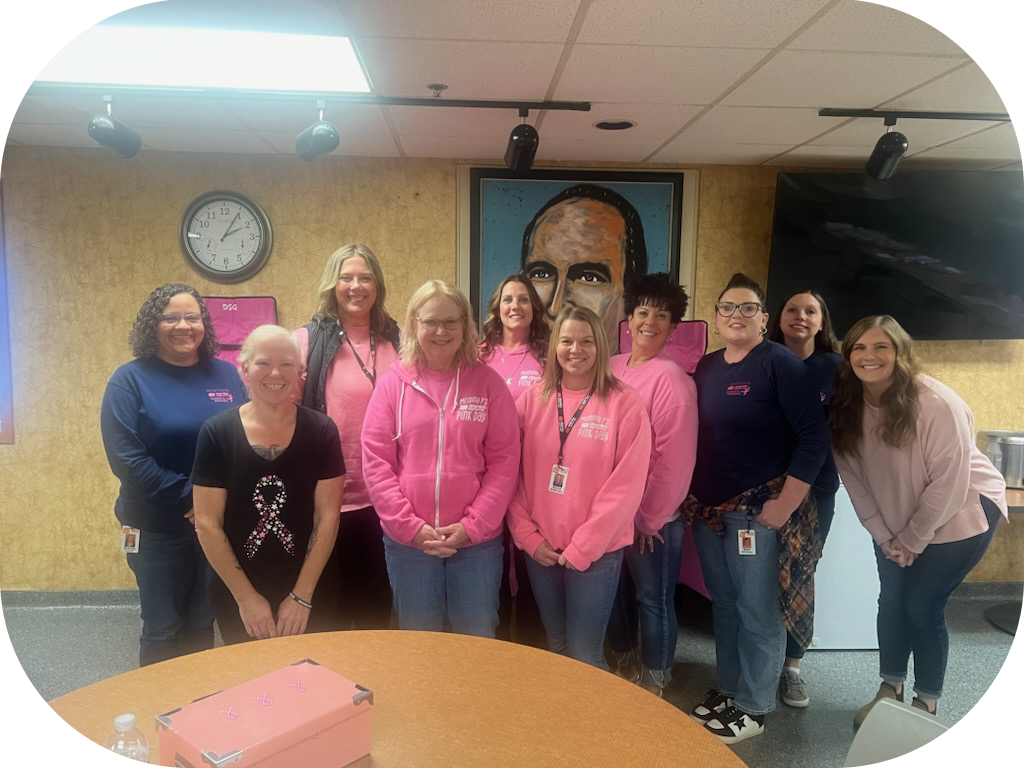
Mexico is joining the Pink Campaign by donating to the CIMI Chihuahua Foundation, which supports various programs for early detection and treatment of cancer. It’s fantastic to see such vital support for cancer awareness and treatment.
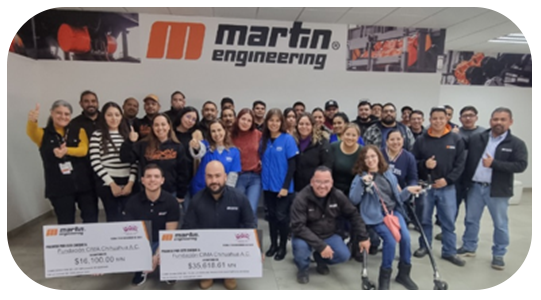
Martin USA sponsored the Black Hawk Welding Invitational, offering secondary school students the opportunity to compete in welding.
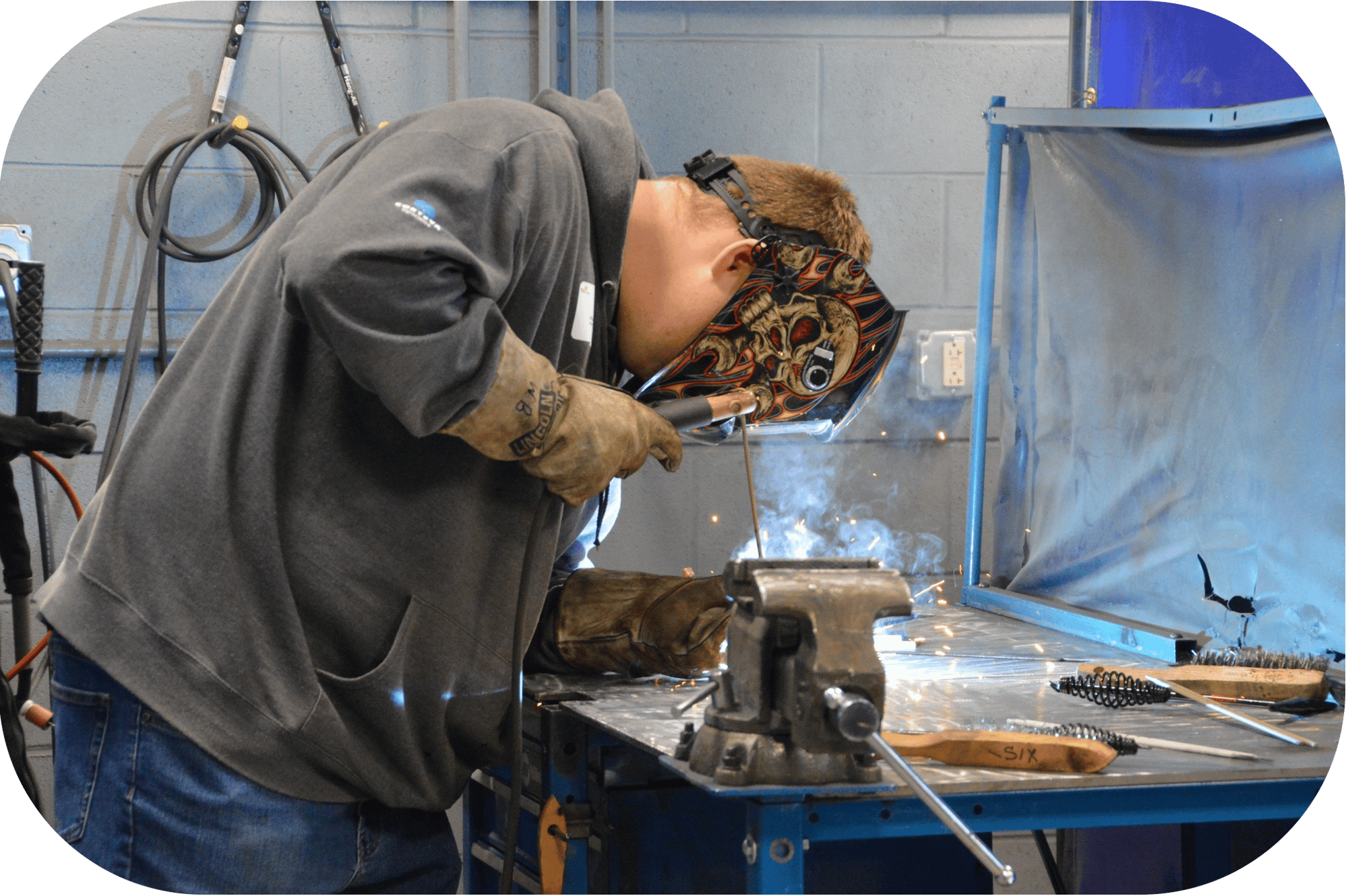
Santa Claus and the Peterson elves recently visited a local grade school/junior high to spread cheer and deliver gifts to each student.
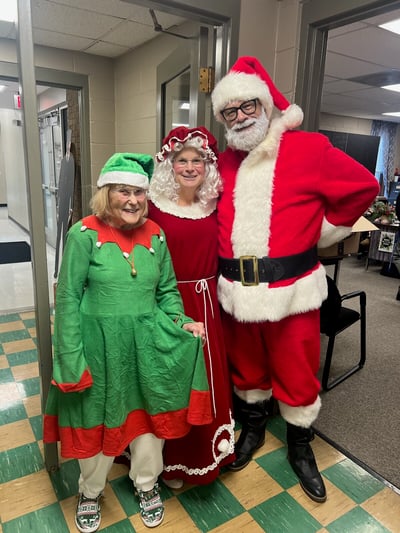
Local Schools and Children's Homes - Around the globe we volunteer at local schools and children’s homes, provide supplies and help to inspire children
South Africa has funded four employees' children with bursaries for their university studies. It's heartening to see such support for education and future generations.
Ronald McDonald House Charities
Local Arts Councils
Various Foundation organizations such as Arthritis, Alzheimer’s, Down Syndrome, etc.
Honor Flight
Fire Department and Ambulances
Shelters for homeless, mental health, elderly, and single women
In South Africa, training was held for 30 employees in Leadership, Management, and best Business Practices. Additionally, there is a program aimed at improving skills by empowering employees.
The MST 360 program was launched in Peru and Colombia to provide 45 hours of training in safety, quality, efficiency, and customer satisfaction. This initiative aims to enhance these critical areas for a more effective and customer-focused operation.
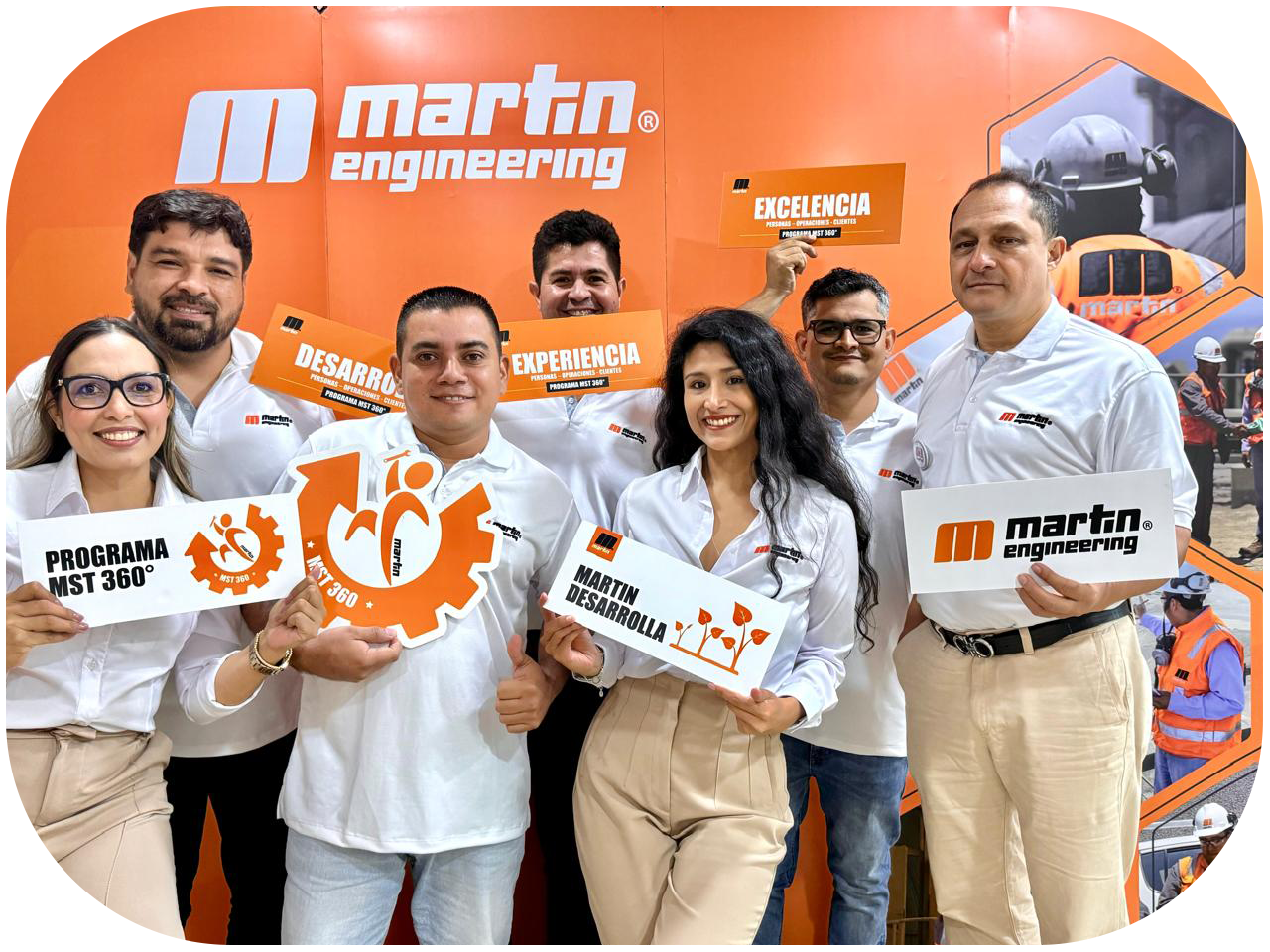
The US has been focusing on apprenticeships, with 5 individuals currently participating in the programs and 1 just finishing. Additionally, emerging leader training has been provided for 8 individuals.
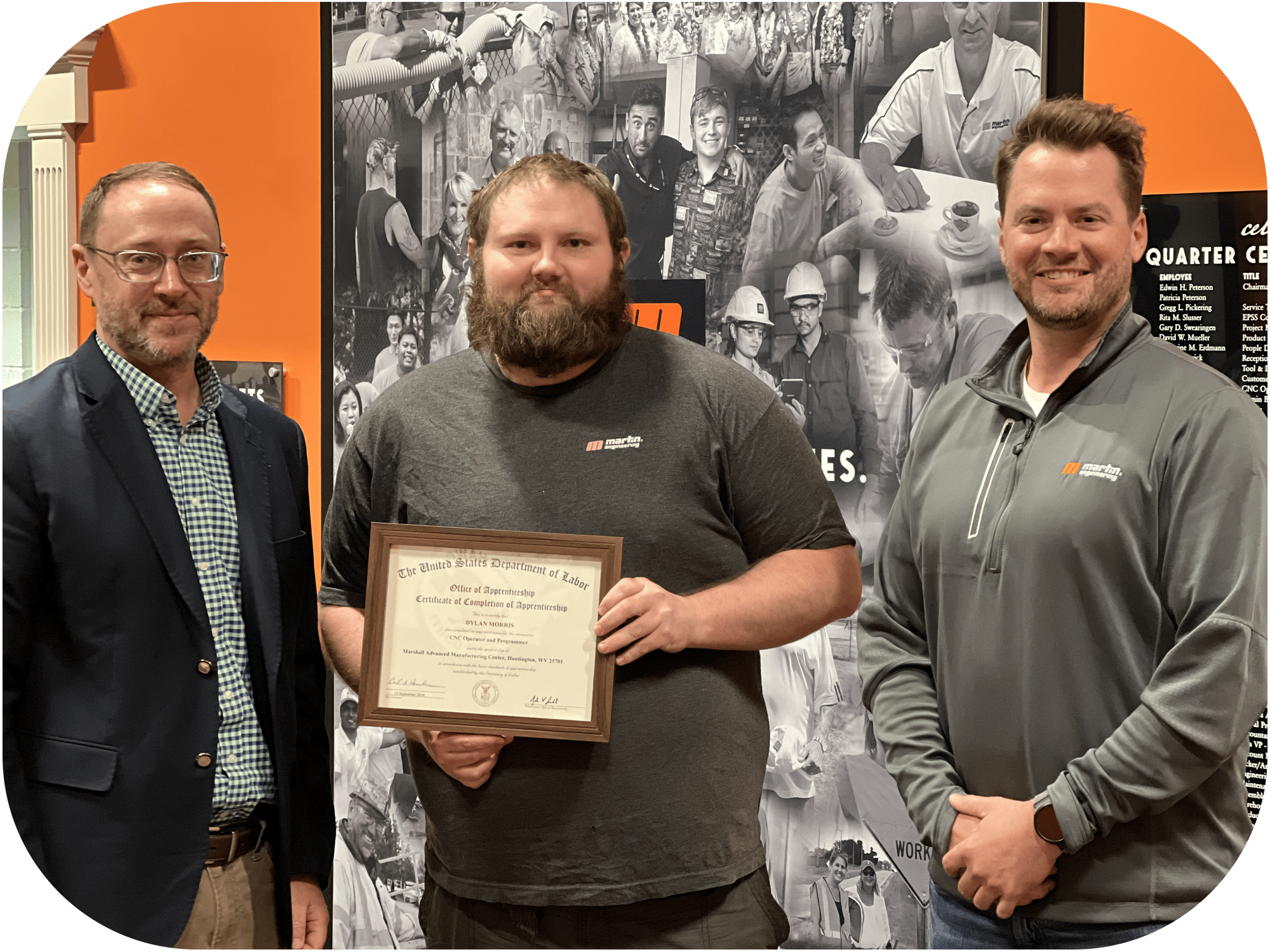
Building the Martin Way is moving ahead, with plans to implement our new ERP in early 2025. The teams are diligently working on different aspects of the project workstreams, development, and testing to ensure a successful implementation in the US before rolling it out to other locations.
In Europe, we have implemented a new onboarding training for the employees, as well as safety and mental health training.
In Mexico, 7 employees are nearly complete with the Development Program and will finish with a university course on leadership. Additionally, Mexico provides educational support to its employees, with nine employees currently participating in this benefit.
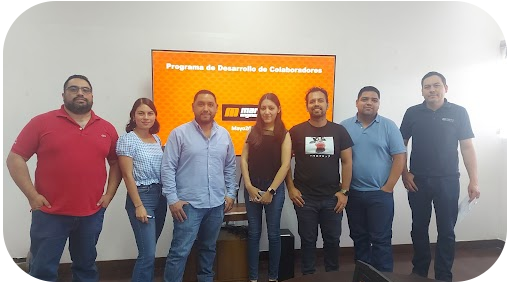
In China, the ongoing employee development program is all about building a brighter future for everyone involved. Investing in growth and development really sets the stage for long-term success and well-being.

We promote a Safety Always culture, which includes awareness and monthly education for all employees. In the USA, all field employees receive onsite product training, confined space training, lockout/tagout training, MSHA/OSHA training, and customer onsite safety training. We track near misses and work to ensure everyone goes home to their families unharmed.
In Europe, we launched both online and in-person safety training for all employees. Globally, we adhere to local safety guidelines, providing comprehensive safety training to all employees and tracking near misses, incidents, and necessary improvements. In South Africa, we hold weekly safety meetings focusing on specific topics such as driving safety, violence, harassment, and visitor safety. Additionally, we host an annual Safety Olympics Day to learn about safety in a fun and competitive environment.
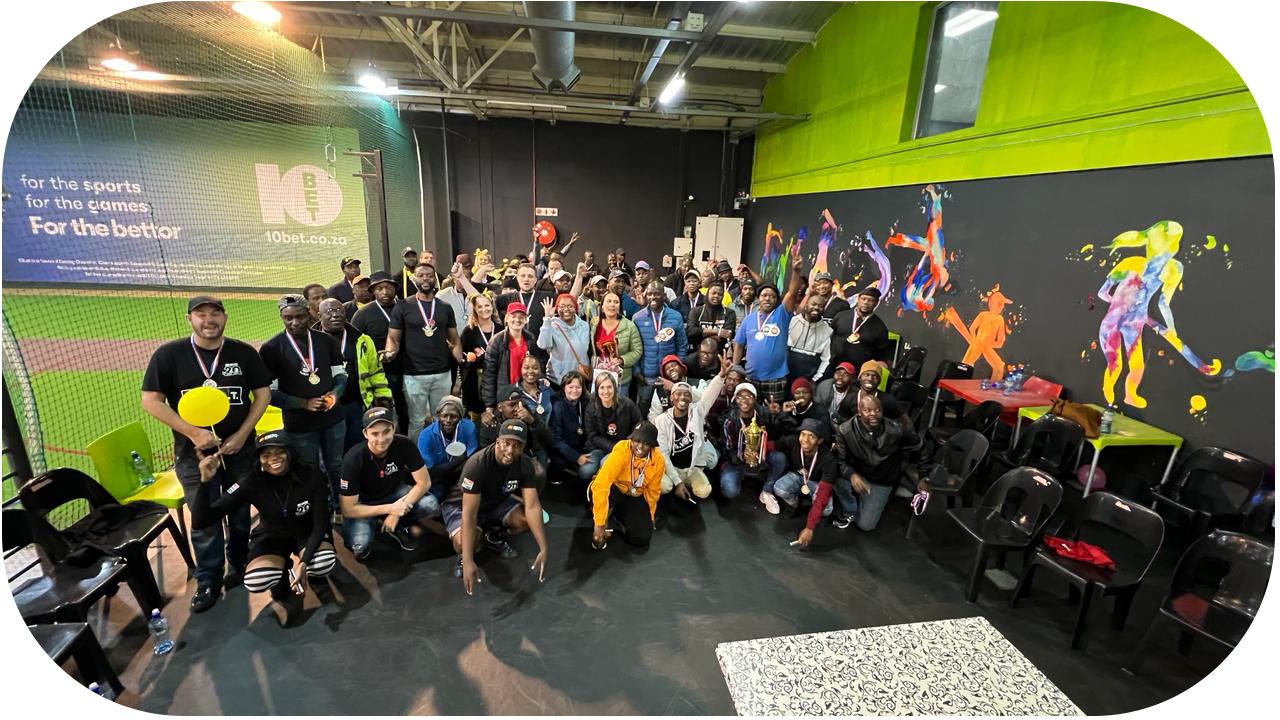
In Brazil, we provided ergonomics training for worker safety. Other units conduct monthly safety training and have elected safety committee members. The "September Yellow Card" campaign is ongoing, focusing on mental health awareness.
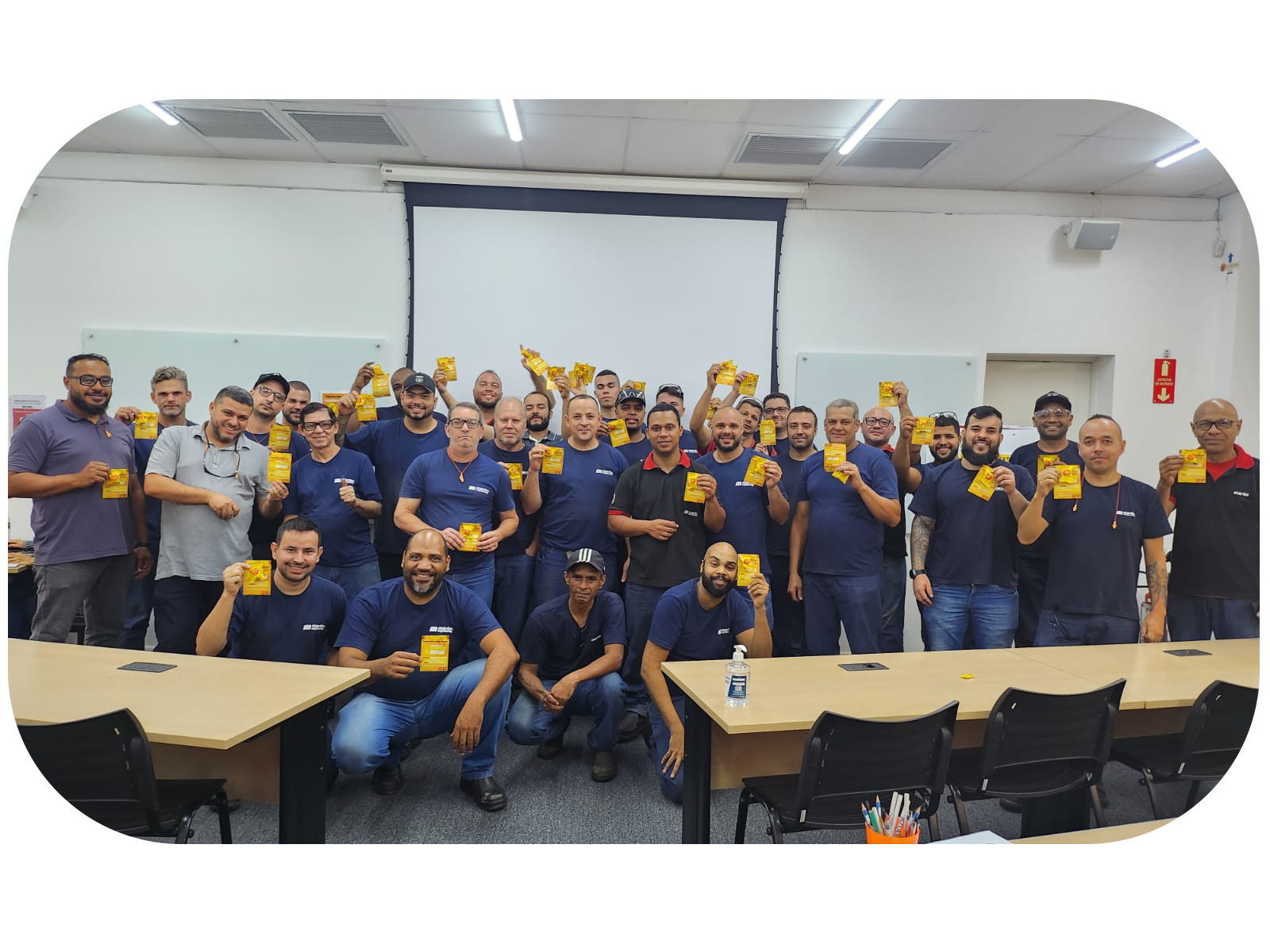
In the USA, we brought all our service technicians in for a weeklong class covering product installation, confined space, lockout/tagout training, and team building.
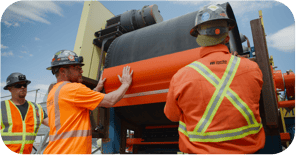
The USA implemented a Safety Hero – Safety Incentive Program with a slogan Find It, Fix It - to promote speaking up when a safety issue is found.
The SLAM (Stop, Look, Analyze, and Manage) approach is a practical and effective method for enhancing safety awareness and practices. By dedicating a week to safety training and commitment, India is taking significant steps towards creating a safer environment.
Peru and Colombia are hosting various safety sessions to promote safety throughout the team, including a session for the Service Technicians
As we celebrate our 80th Anniversary with our community and our families
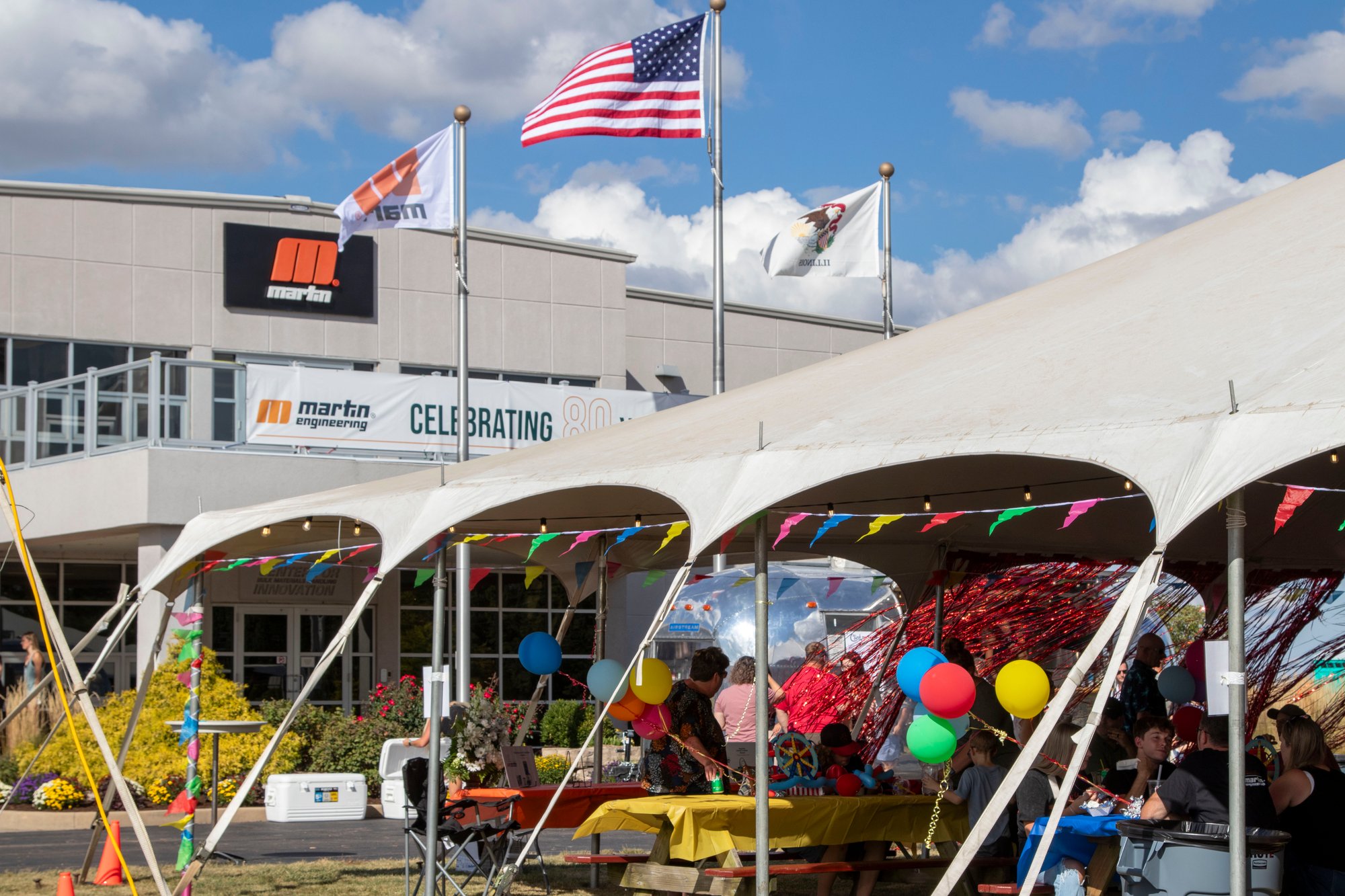
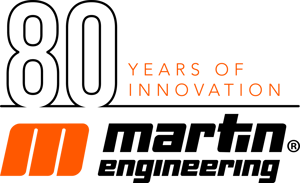
Our unit in Brazil will celebrate 35 years in December
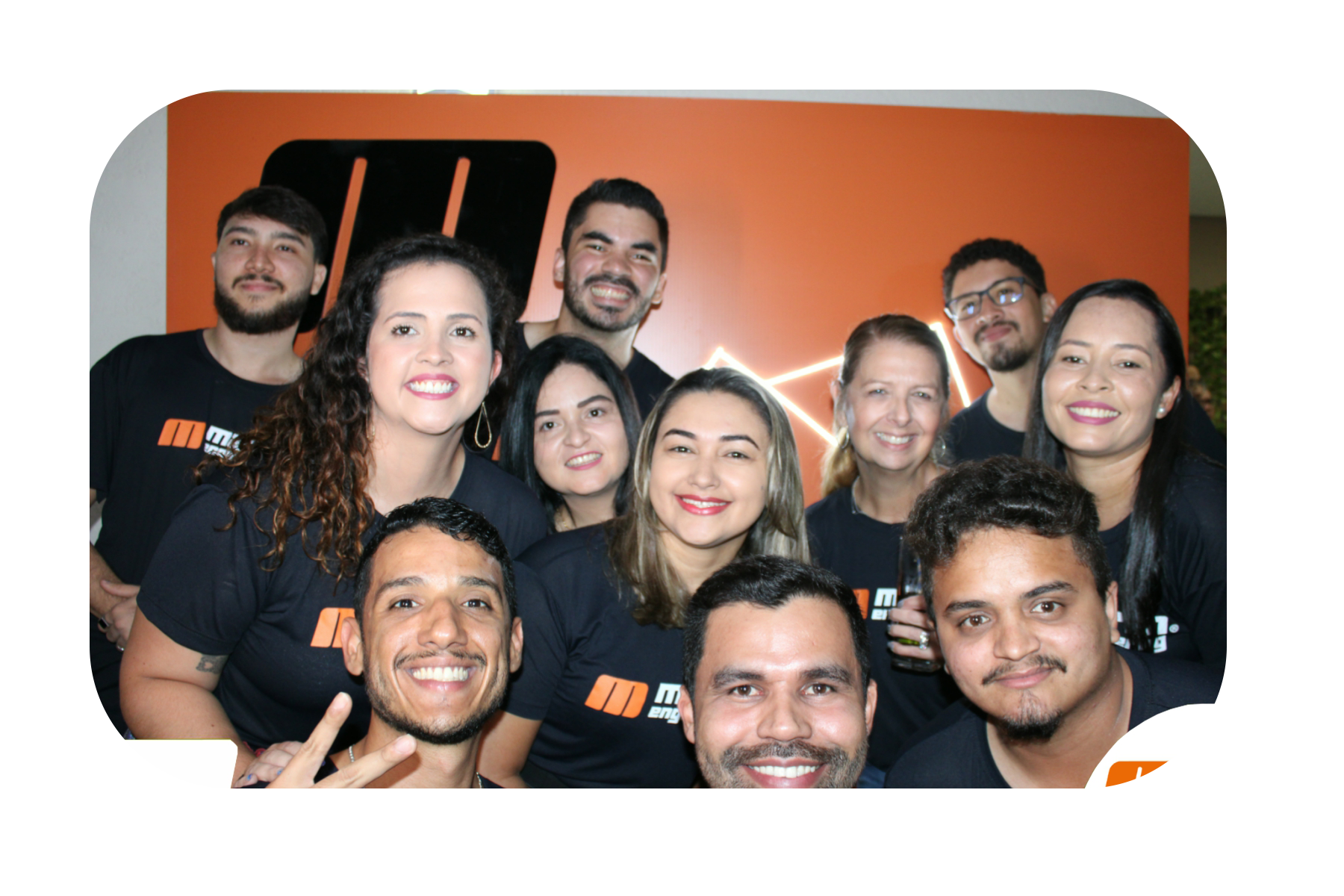
.jpeg?width=1600&height=1066&name=WhatsApp%20Image%202024-12-16%20at%2011.25.42%20(1).jpeg)
Service Awards – We continue to celebrate our employees for their loyal service, starting at 5 years. We now have 47 individuals in our Quarter Century Club, dedicated to 25 years of service.
The USA Wellness Squad has offered various events throughout the year, including walk/run events, a Biggest Loser weight loss challenge, and a self-defense class.
Several other units host wellness days regarding healthy lifestyles, prevention talks and other topics.
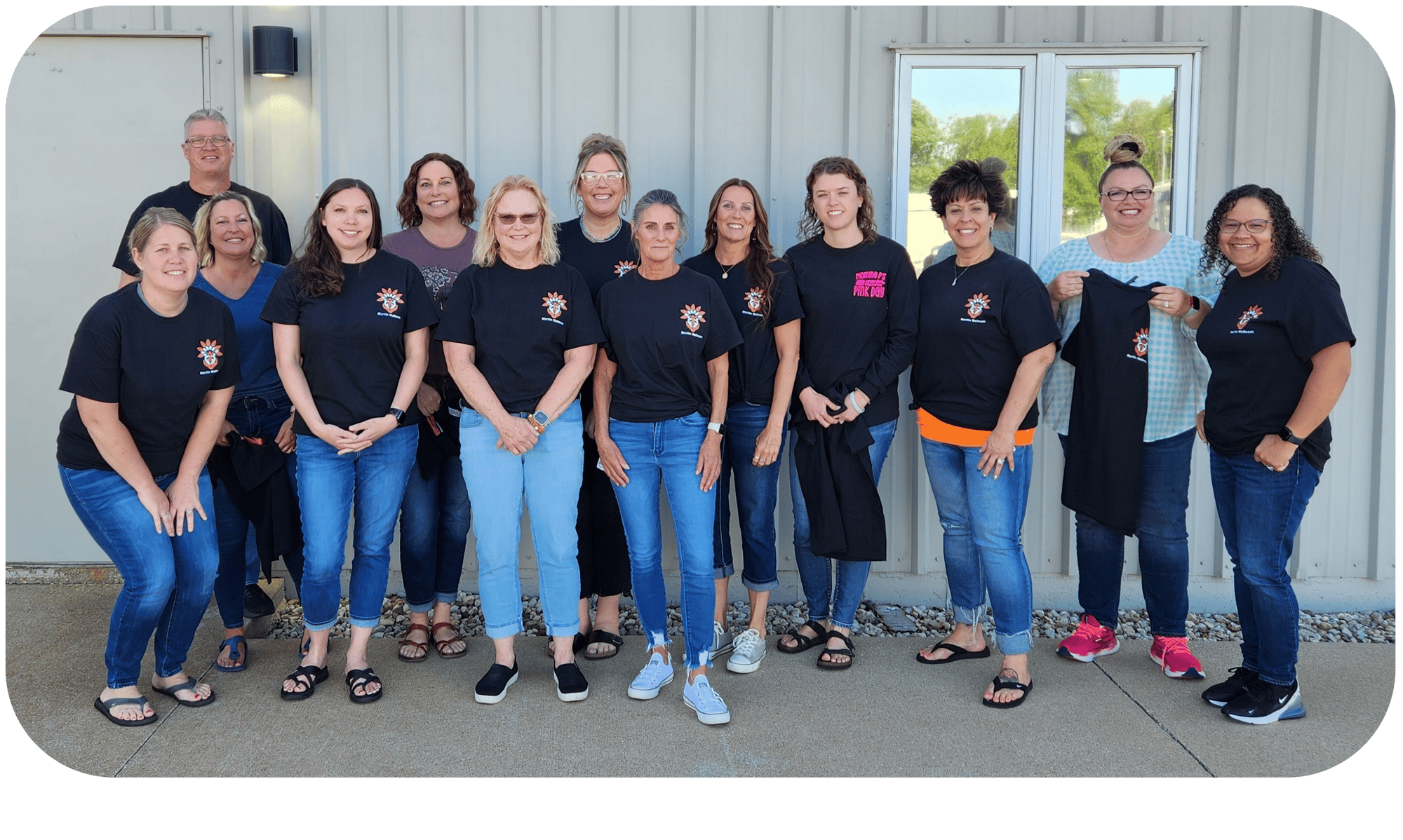
Globally, we have a diverse workforce with multiple nationalities, regions, and races. We are an equal opportunity employer, dedicated to attracting employees from all different backgrounds. Currently, 20% of our staff is female.
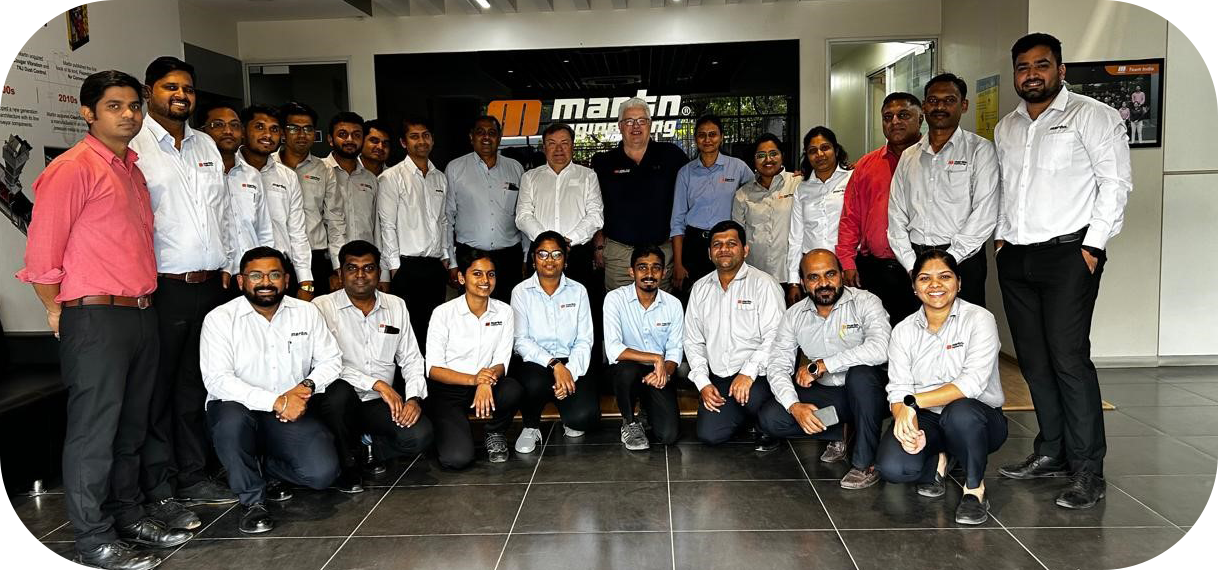
Maruschka has been with Martin for 10 years, with an impressive and growing trajectory. With a degree in Production Engineering, she began her career in 2014, working on the Service Contract at Salobo Metais. In 2016, she transitioned to the commercial area, where she stood out as a Sales Engineer. Her remarkable performance led her to be promoted to Regional Sales Manager in August 2024, a role in which she leads a team of 11 people with excellence. Together, they serve and generate business at Vale's three main plants.
Her dynamic and enthusiastic approach, combined with her knowledge of the client's processes, make her a leader who inspires her team to achieve results.
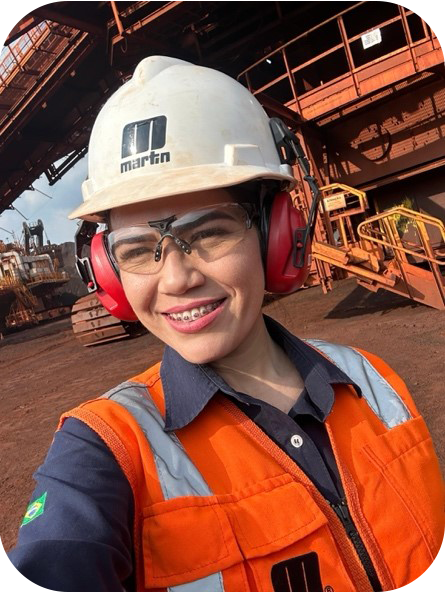
Marina holds a degree in Materials Engineering, specializing in Maintenance Management, and has one year of experience at Martin. She began her career at the company as a Shift Supervisor, working on the Vale S11D Service Contract. Her performance and dedication led her to be promoted to Contract Supervisor in September 2024, where she leads a team of 70 people on the largest service contract in Brazil.
Marina is a resilient professional who values teamwork and building a collaborative environment focused on delivering the best results.
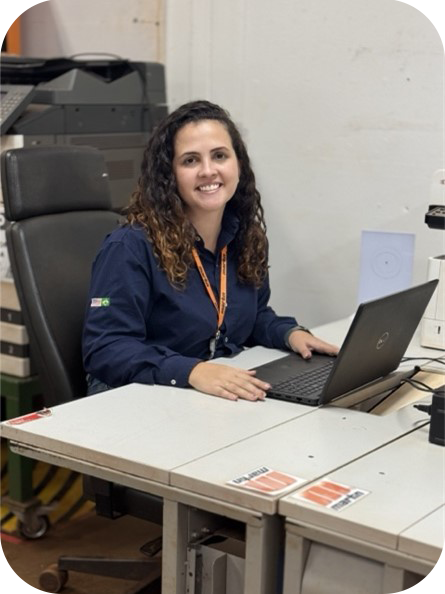
Ashwini has been with Martin for 11 years and started as a Design Engineer. She received promotions to Project Leader and Conveyor Products Specialist over the years. In these roles, she presents Foundations Seminars to customers and provides technical expertise. In 2024, she was
promoted to Sales & Marketing Head EMEAI to improve processes and sales and marketing efforts. In this role she enjoys collaborating with the regional team and experiencing the different cultures.
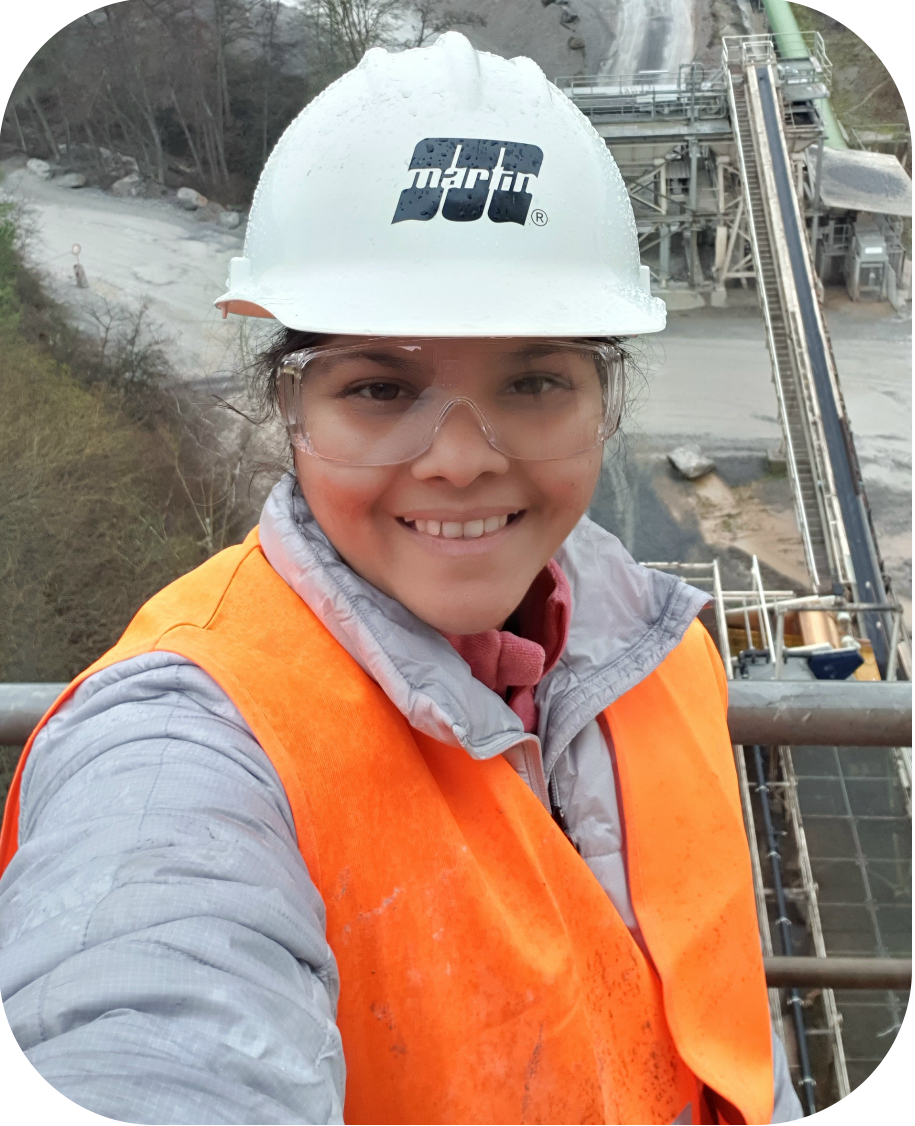
Board/Management: A diverse board governs us, consisting of two internal members, a family member, and three external board members. The external directors have extensive business governance backgrounds across multiple specialties. The board has a diversity of 50% women and meets four times a year.
Audit Committee: We have an outside audit firm that reports to the two-member Audit Committee, with one board member being an SEC-qualified expert.
Leadership: Our CEO, CFO, Directors, and Area Vice Presidents strive to manage risks, evaluate budgets versus sales, and ensure growth that meets the needs of all stakeholders.
Martin in the US and Colombia are proud members of the United Nations Global Compact organization, adhering to the ten principles based on human rights, labor, environment, and anti-corruption.
Policies: We have comprehensive policies covering Foreign Commerce, Export Compliance and Ethics, Diversity, Conflict of Interest, Privacy, Anti-Harassment, and Cyber Security. Employees are required to sign off on certain policies annually, and any modifications are communicated clearly. Some policies require an annual review by employees.
Export Compliance: We have a worldwide process for reviewing our export compliance risk.
We have an outside service available to all employees, allowing them to report any illegal, unethical, or unsafe business practices or conduct.
Diversity: We have a policy in place to promote diversity and inclusion at every level, while adhering to all local requirements.
Compliance: We are ISO 9001:2015 certified, ensuring our product safety and risk management standards are met. Our New Product Introduction process includes thorough product tests and safety evaluations, and we have a product rationalization process in place.
Contract Review: We have a contract review process to manage risk and alert our teams to any unusual terms.
Supplier Evaluation: In the USA and other locations, we evaluate new suppliers and have surveyed our top 20% of suppliers in the areas of stewardship, safety, HR policies, and conflict minerals.
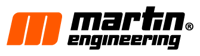