Eliminate Airborne & Respirable Dust
By preventing dust at its source, it can't escape.
Dust Management Basics
Simple tactics can be incorporated into your operation to reduce and even prevent airborne dust.
When material transfers from a conveyor belt or hopper to a conveyor belt, it is crushed under its own weight and exposed to airflow, creating opportunities for dust. Dust creates a harmful environment for those working around it, environmental concerns, and increased scrutiny from neighbors. OSHA and MSHA have targeted efforts accompanied by steep fines to reduce dust. Most facilities don’t fully understand the underlying issues causing dust and therefore, don’t know how to properly solve them. Many facilities focus on dust suppression and collection which are advantageous but it is more beneficial to focus on dust containment. Dust should be controlled at its source of creation. Control dust at the transfer point by controlling the air associated with the material being transferred. By controlling the air, dust is therefore controlled.
Root Causes:
- Influx of air as the transfer point loads with material
- Material degradation increases small fines
- Poor transfer point design for current production expectations
Best Practices:
- Support the belt the entire length of the chutewall so it doesn’t sag away from skirting
- Protect rubber skirting with an abrasive-resistant steel wearliner
- Install belt skirting to seal air
- Utilize suppression and collection only after containment has been achieved
- Slow the exiting air velocity to under 200 FPM with a dust curtain
To properly reduce dust, one must understand and execute the mechanical points of dust containment.
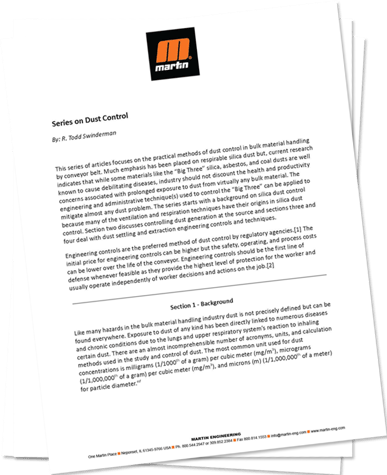
Dust Control White Paper
by R. Todd Swinderman, PE
Airborne dust is a nuisance that can quickly get out of hand, causing severe consequences such as health concerns and regulatory noncompliance. There are practical methods for controlling dust arising from conveyor belts handling bulk materials. Reducing dust at its source can be challenging but it leads to long-term success.
Case Study
Problem
Orlando Utilities Commission – Stanton Energy Center (SEC) is one of Central Florida’s leading environmental stewards, meeting or exceeding all air permit limits with advanced pollution control equipment. When company officials decided to upgrade the dust containment on one of its primary coal conveyors, they contacted Martin Engineering. They wanted to increase the safety aspect by limiting dust and spillage from one of its principal conveyors, engineers wanted to reduce airborne particles and eliminate a potential source of trips and falls. They also wanted to reduce clean-up and maintenance time, allowing critical manpower to be utilized elsewhere and improve plant efficiency. Additionally, preventing coal dust spillage would help minimize wear on rollers and other moving components, saving on replacement part costs and labor.
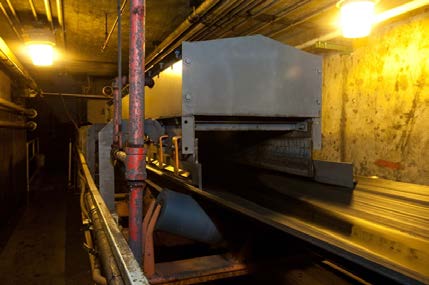
Solution
To address the situation, Martin supplied and installed a number of upgraded components, including Martin® Double ApronSeal™ Skirting, which employs two wear surfaces on a single elastomer sealing strip installed along the bottom of the skirtboard in the loading zone. Martin also installed an impact cradle to better absorb the force of the falling material and protect the belt and structure. In Addition, a Martin® Slider Cradle was added under the skirt board to better support the edges of the belt and eliminate sagging. To maintain precise centering, Martin installed a belt tracking system for immediate, precise adjustment.
Finally, Martin installed a high-efficiency insertable air cleaner with an explosion-proof motor. The Martin® Air Cleaner can eliminate many of the problems seen with central “baghouse” collection systems; they help solve airborne dust problems by keeping fine particles in the load or returning them to the material stream.
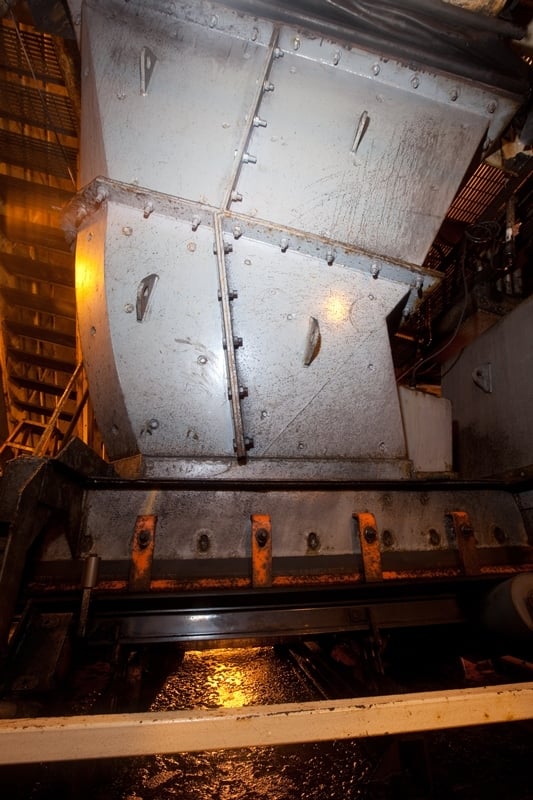
Results
The improvement was immediate. “It’s not just the savings in cleanup time, but also in preventing the idlers from wearing our prematurely. Now I don’t have to send my guys out there to replace those failed components, so it saves on labor and replacement parts, as well as the housekeeping time,” said Material Handling Supervisor Stuart Cason. “No question the system has paid for itself. We used to spend a lot of time making adjustments and repairs, but since the install, the system has been essentially maintenance-free.”

Webinars
Passive Dust Control
Reducing Dust and Spillage
Maintenance
Blog
What happens when dust suppression and collection aren't the answer?
by Jim Bess
Some common questions I often get asked are “how much is a dust collector” or “how much would it cost for a dust suppression system?” My response is always the same. “I can’t answer that question.”
Many times, people can’t understand why I won't give them at least a ballpark figure. A few days ago, I had someone ask “are we talking $1000 or $100,000?”
We would be doing a disservice to our customers by trying to throw a dollar amount at a problem we haven’t properly diagnosed. Many of the issues material handlers want to correct with suppression or collection end up not needing either. More often than not, the problem can be corrected by making some changes to how the belt is supported and/or sealed throughout the load zone.
Containment is truly the foundation of a clean conveying system
Another reason we need to diagnose the actual problem is that sometimes the actual cause or source of dust is not exactly located at the point where the problem is found. There is no reason to spray countless gallons of water on a conveyor belt head only to realize you haven't even touched the problem and that the dust is actually falling from above or coming from a different location.
Our experts can diagnose these problems, making sure the solution is the easiest and most effective way to actually fix the problem. Many times, it’s going to be much more cost-effective than throwing the “biggest dust collector you have” at the problem.
A similar conversation happened just the other day as a guy was certain that he needed some sort of dust collector installed near the exit of the load zone on one conveyor. He was somewhat surprised by the fact that I didn't want to take a guess as to what the cost of this solution would be. I finally convinced him to let one of our field reps come take a look at the belt, and I promised him we would get him a real estimate.
Here is what we found after the inspection:
-
The belt was properly supported
-
Adequate wearliner was installed
-
The belt skirting was in good shape
-
After checking the airflow, a dust collector was not necessary or the correct solution
Our solution
We installed an additional slider bed to further support the belt, skirtboard, wearliner, and skirting to seal the belt, and two dust curtains to slow the airflow and allow dust to settle back into the material stream. It resolved the dust problem and was much more cost-effective than adding a collector.
On the other hand...
Many times collection and suppression are valuable additions to an operation. When specified and installed correctly, dust collection and suppression can greatly reduce, sometimes even eliminate, airborne dust.
Understand the problem first, solve it second
A proper and effective solution all comes down to a proper and thorough understanding of the problem, from the obvious signs and symptoms to the sometimes more subtle root causes. This is where knowledge and experience can prove invaluable in providing insight and helping make the right decisions to effectively correct the problem.
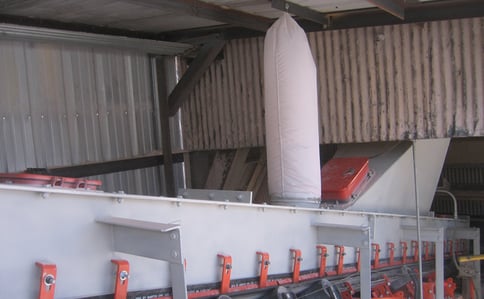
Martin Engineering manufactures active dust filtration systems that use a fan to force air through a filter medium above the conveyor loading zones, as well as passive systems that do not require a fan.
Both types of filtration are designed to collect dust particles so they agglomerate into larger particles, which are returned to the material stream. Because these systems feature a compact design, they fit into tighter spaces without sacrificing effectiveness.
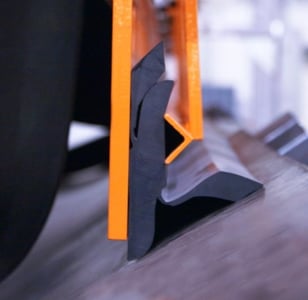
To help you contain dust, Martin Engineering manufactures products that minimize the amount of fugitive dust that becomes airborne in the first place. This prevents the hazards caused by runaway dust – such as the risk of the dust igniting and causing an explosion, or the health issues that can result from dust inhalation – by stopping it at the source.
Martin manufactures a wide range of transfer point options specifically engineered to stabilize the belt and seal it at the skirtboard, preventing dust from escaping and returning it back to the material flow.